BMB goes electric at K 2016
This year, just as it does every three years, BMB will be coming to the K fair in Düsseldorf with the latest innovations from its product range, which are the result of its ongoing close collaboration with processors and its hefty investments in research and development programmes. Given that electric machines now account for around 90% of the injection moulding machines sold by the Brescia-based manufacturer, its participation at the German fair will focus on production cells capable of operating with very short, extremely precise cycle times, which consume around 45 to 60% less electrical energy.
All eyes will therefore be trained, in particular, on the eKW Full Electric series, now available in 100 to 1,150 ton versions and offering the speed and precision typical of hydraulic injection presses for packaging applications, but with some added advantages. Mindful of the growing awareness of the need for environmental protection, the BMB designers have managed, by eliminating the use of oil for the machine’s motions, to combine the performance levels allowed by the KW toggle-joint system with a dramatic reduction in energy consumption, as well as in the noise and dirt levels. The switch from hydraulic to electric drives has also made it possible to improve the setting of the operating positions and reduce the size of the machine. All the motors used on the eKWs are driven and managed by a computerised numerical control (CNC) for machine tools, and this has allowed BMB to obtain centesimal precision without having to reduce the speed of the movements.
The drives, which are interconnected, recover the
braking energy, thereby increasing the energy efficiency of the machine. The
system, fully integrated into the drive and control functions, makes it easier
to find the set positions and ensure perfect compliance with all the operating
cycle values. The positioning procedures is now greatly simplified, requiring
the setting of just three values: position, speed and force.
All the rest is taken care of by the machine itself, which reaches the set positions with centesimal precision, automatically adjusting acceleration and deceleration rates. Monitoring and measurement of energy consumption are both offered as standard functions on all the models in the series, allowing instantaneous and continuous readings of the kWh consumed for each kg of material processed. Another standard feature is the remote control of the machines, made possible by the Remote Desktop software integrated in all the models.
The company will also be unveiling two fully electric models in Düsseldorf. eKW16Pi/480 Full Electric, which belongs to the Pi series, is the smallest machine in the range and it is specifically designed for the high-output moulding of thin-wall items. During the fair itself, the machine will be working with a 4-cavity mould and IML robot. The machine will be producing 155 ml food containers weighing 6.2 g; the total shot weight will be 24.8 g and the cycle time 3 seconds.
eKW40Pi/1300 Full Electric, on the other hand, also belonging to the Pi series, is a machine with a 400-ton clamping force used for packaging production, a sector that demands high performance in terms of speed and accuracy. For this reason, the Pi series offers direct movements on all axes, thanks to torque motors on the injection unit and brushless ones on the clamping and demoulding unit; both these motors are coupled directly to the axis to be moved, with no interposed driving belts or gears. At the fair, the machine will be shown producing 300 ml food containers; it will be used with a 6-cavity mould and a side entry robot for removing the mouldings; the cycle time will be 3.2 seconds.
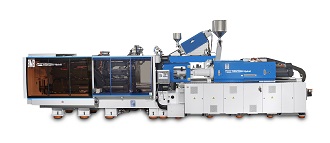