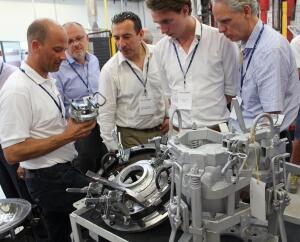
Si chiama Smart la nuova gamma di impianti per lo stampaggio rotazionale annunciata da Persico il 18 giugno in occasione della presentazione dei risultati del progetto Rotofast, che ha visto coinvolta la società di Nembro (Bergamo), insieme a vari partner italiani ed europei. Il primo esemplare di macchina sarà pronto tra fine agosto e inizio settembre, mentre il lancio ufficiale avverrà al K 2013 (Düsseldorf 16-23 ottobre). La gamma è nata dell'unione della tecnologia rotazionale convenzionale e del sistema Leonardo, sviluppato sempre da Persico, allo scopo di accrescere le potenzialità di mercato del rotostampaggio allargando il ventaglio dei materiali speciali lavorabili.
Le macchine risultano simili a quelle tradizionali a braccio singolo e gli stampi in alluminio, ottenuti mediante CNC, presentano uno spessore da 5 a 10 mm e sono dotati di apposite scanalature per l'alloggiamento delle resistenze elettriche con cui vengono riscaldati. Gli stampi sono anche dotati di sonde per il rilevamento della temperatura, di dispositivo di raffreddamento interno e di tutti quegli accorgimenti richiesti dal sistema Leonardo per il controllo di processo. Inoltre, sono predisposti per l'utilizzo di meccanismi di apertura e chiusura automatica e presentano 16 zone di riscaldamento, che permettono di raggiungere una potenza massima di 100 kW. Il cambio rapido degli stampi consente di evitare il fermo macchina durante questa operazione. Il sistema Leonardo per il controllo automatico del ciclo di stampaggio si basa sulla temperatura dell'aria all'interno dello stampo e il ciclo di produzione viene monitorato da un PLC, su cui sono stati preimpostati tutti i parametri.
Il riscaldamento elettrico rende superflua la presenza di unità di riscaldamento e raffreddamento, riduce il peso complessivo dello stampo, abbatte il consumo di energia senza limiti di temperatura per il processo, e accresce l'efficienza del riscaldamento. In termini di prestazioni, è possibile raggiungere picchi di temperatura di 350°C e il riscaldamento risulta più uniforme, nell'ordine di ±5°C, con una distribuzione ottimale in tutto lo spessore dello stampo; è più rapido, con un incremento della temperatura da 70°C a 220°C in circa 4 minuti. Anche il raffreddamento, ottenuto con ventilatori localizzati o dispositivi Venturi, risulta più uniforme ed esente da possibili deformazioni degli articoli prodotti; è anch'esso più veloce, passando da 220°C a 70°C in 7 minuti circa, e può essere interrotto a temperature specifiche.
L'impianto presenta un layout compatto e flessibile e può essere fornito con controllo della pressione interna e dispositivo del vuoto opzionali. Il processo risulta efficiente, ripetibile e veloce. Tra i possibili campi applicativi rientra la produzione di articoli tecnici con tolleranze ristrette e geometrie complesse, di componenti estetici e il costampaggio di inserti metallici.