The world's biggest gasket is Italian
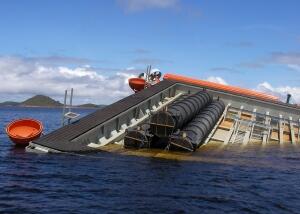
The Italian Oldrati Group has designed and constructed the world's biggest rubber gasket: 22 metres wide, weighing 100 tons, and ensuring a mechanical strength of 37 kg per square centimetre, it will be used for the maintenance of the Guri Dam. The gigantic gasket, made up of various moulded parts that are fitted together like a puzzle on site, will make it possible to isolate the dam's bulkheads and therefore guarantee the maintenance technicians safe access, for the first time ever, from the submerged side. Made from special materials, it exerts 45 thousand tons of sealing force in contact with the concrete, eliminating even the tiniest infiltrations that could lead to an implosion due to decompression.
Built in the 1960s on the Orinoco River in Venezuela, the dam, which is 1.5 miles wide and 90 metres deep, is the second largest in the world. The first of a series of four, it needs to work at full capacity, but wear over time meant that it was being used to only 30% of its capacity, a situation that was having repercussions on other structures and on the whole country's electricity supply. Hence the Venezuelan government's request for a specific solution that would make it possible to carry out maintenance work directly on the walls of the dam. Oldrati was drawn into the project by GSE, a company based in Trieste that designs and manufactures professional underwater equipment and is the only company in Italy to produce mini-submarines.
The project, named "Compuerta flotante submarina", involved the construction of a square underwater door (a world first) of the same size as the mouth of the dam, isolated thanks to the perfect adhesion to the concrete and the high sealing force allowed by the self-propelling effect and the gasket; this ensured that the necessary manoeuvres could be accomplished and that the technicians could gain the necessary access in absolute safety. In addition to this door, the order, worth 50 million euros, also included the use of a small supervisory submarine as support, capable of reaching depths of up to 165 metres with three technicians aboard.
Tests on the seal, which included the application of crushing pressures of up to 1500 tons per square centimetre, were conducted at the Oldrati facilities. These tests, carried out in the presence of highly specialised technicians, focused in particular on the seal at the junction points between the individual pieces, in order to ensure optimal adherence and absolute safety. Everything is now ready and waiting for authorisation to proceed. Moreover, the project is also awaiting international approval to be used in series in the future.