Special screw elements for elongational flow
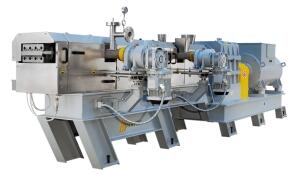
Corotating twin screw extruders customised and configured according to the individual processor's needs are now delivered by Maris on the basis both of a proprietary know-how acquired during its fifty-year activity and the in-house designing and manufacturing of each single mechanical item. An example of such versatility is represented by the production of masterbatches, one of the most common applications of its extruders.
In this field, the optimisation of the process cycle is obtained thanks to a vast range of solutions involving not only the process parameters but also the geometry of screws, with the choice of the best L/D ratio and profile. Thanks to an experimental research aimed at optimising the compounding stage in order to get the best possible quality masterbatch, the manufacturer has been able to develop special screw elements that make it possible to generate an elongational flow.
This type of flow, which is not present in sizeable portions of the process zone, proves particularly effective in the compounding stage and is normally obtained by means of chaotic flows generated by the screw's geometry. Using the Maris Pressure Index (MPI) - an analysis method patented by company to analyse a pure masterbatch that can generate a screen clogging curve - it has been possible to compare the results obtained with a standard and an experimental screw profile, respectively.
A less frequent clogging of the filter and, therefore, a higher quality of the masterbatch is indicated by a lower increase in pressure during the measurement step. As a consequence, during the analysis it was found that the material produced with the experimental screw profile gave a better outcome than that achieved with both the standard profile and the reference profile used in the research tests.