Experiencing the full control
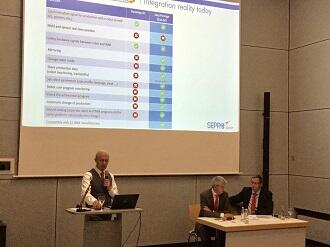
Under the motto “Experience Full Control,” Sepro Group has exhibited at Fakuma 2018 a total of 21 robots, including 8 operating on its own stand and more than a dozen on the stands of injection-moulding machine manufacturers.
“At Fakuma, our focus is on control”, explained Jean-Michel Renaudeau, CEO. “Our customers use the Visual control to operate their robots, and by using robots to support their human workers, they also gain greater control over the quality of the parts they make, their plant productivity and their company profitability. More than that, however, we offer them full control through our commitment to do whatever we can to help them improve their operations and find successful solutions to process challenges. Our customers are the driving force behind what we do. In all their interactions with Sepro, we want them to experience full control”.
For the first time, the Sepro display featured not just one, but three operating IMMs with robot control fully integrated into the machine control. Two of the machines were provided by Sumitomo Demag, Sepro’s oldest OEM robot partner, and the third was from Zhafir Plastics Machinery (a brand of Haitian International), a recent addition to a list that now includes nearly all of the biggest brands in moulding machines. One of the Sumitomo Demag machines 180-ton IntElect machine with a new high-speed 3-axis robot developed by Sepro for Sumitomo Demag. A Success 5 robot, the smallest Sepro makes, operated (also with an SDR label) on a 100-ton IntElect machine. Finally, a 60-ton Zhafir Zeres IMM was equipped with a Sepro 5X 15. The premium 5X robot family combines the versatility of Sepro’s 3-axis Cartesian platform with the precision of a 2-axis Stäubli wrist.
Elsewhere on the stand, three examples from Sepro’s popular Success range of 3-axis general-purpose robots - the Success 5, Success 7, and Success 11 - operated together with an S5 Picker, which has a 3-axis mechanical design similar to the Success robots. The Success range can equip IMMs from 20 to 700 tons, offering plastics processors economical and reliable productivity in typical pick-and-place and stacking applications.
New choices in collaborative robots
Sepro enters the collaborative robot (cobot) market with a “collaborative robot solution” that is quick and easy to deploy, lower in cost and more productive than most conventional cobots. Called Seprobot, the package combines a Yaskawa 6-axis robot with sensor and physical guarding in a fully integrated human safety system. Although it operates in a guarded space, operators get safe access for feed-in and feed-out through openings protected by sensors, light curtains, or other safety devices. Most of the time, the robot operates at full speed, slowing down or stopping only when humans enter the guarded space and returning to full speed when they depart. This enables the Seprobot to operate two to three times faster than a typical cobot.
Integration, optimization and automation
A special section of the Sepro booth at Fakuma 2018 was dedicated to the Open 4.0 philosophy, which stands behind the company’s vision for the “Factory of the Future”. Visitors could get hands-on experience with the Visual control platform. Among other things, this easy-to-use robot control, which was developed by Sepro especially for injection moulding, makes it possible to integrate robot controls with those of the IMM. This kind of integration supports Sepro collaboration with the growing number of OEM partners who want to offer advanced robot and automation options to the processors who purchase their moulding machines. Working with these IMM partners, Sepro has proven to be reliable when it comes to integration. From mirroring the robot control to fully embedded it in the IMM control, Sepro Visual is an open and transparent system, both to our users and to different robot technologies.
Attendees could also view the company’s latest control developments like OptiCycle, a control plug-in (developed in open collaboration with a key customer) that automates robot cycle optimization, and Live Support, an app that links customers and their robots with troubleshooting assistance. Both are intended to function with the Sepro Visual control platform on new and existing robots.
Elsewhere on the stand, a video presentation features the “Solution by Sepro” concept and visitors were able to manipulate 3D renderings of actual automated moulding cells that are typical of these projects. They often involve multiple robots and specialized end-of-arm tooling (EOAT), plus a variety of feeders (bowl, drawer or manual), inspection devices, cavity separation, degating/trimming, box filling and other equipment - all customized to suit specific manufacturing objectives. The Solution by Sepro program provides injection moulders with equipment, engineering expertise and additional services needed to bring new levels of efficiency and quality to their process.