Wider applications thanks to improved weldability and transparency
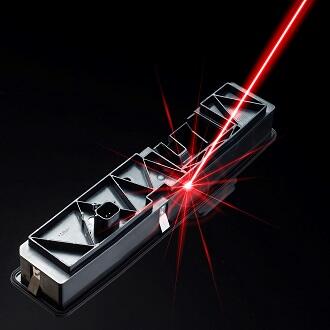
Laser transmission welding - also known as laser welding - is a method employed for joining plastic parts. It enables even very small components with complex geometries to be produced in a cost-efficient and resource-friendly manner, making it part of the growing trend toward the miniaturization of electrical and electronic functions. This is why Lanxess has developed a wide range of laser-weldable polyamides and polybutylene terephthalates (PBT) Durethan LT and Pocan LT (Laser Transparency) and has recently expanded its range to include three new compounds.
At K 2019, the High Performance Materials business unit showcased these innovative compounds. “In addition to good, process-safe laser-weldability, the three new materials possess a range of other important properties that allow them to be used in a broader range of applications,” says Claudia Dähling, an expert in technical plastics at Lanxess. “Potential applications include components for electrified vehicle drives and driver assistance systems as well as devices for digitalizing the world in which we live: the Internet of Things.”
High hydrolysis stability but still good weldability
Pocan B3233XHRLT (currently Pocan TP155-002) is a new, 30-percent-glass-fiber-reinforced PBT compound that exhibits good laser transparency and an excellent resistance in a hot and humid environment. Materials like these are almost unprecedented on the market because standard additives for hydrolysis stabilization generally cause the laser transparency of PBT to deteriorate significantly.
The outstanding hydrolysis resistance of the trial product from the latest Pocan HR generation has been demonstrated in the SAE/USCAR-2 Rev. 6 long-term tests of the American Society of Automotive Engineers (SAE). “This test on the finished part is recognized worldwide as the ultimate test of hydrolysis resistance. In a series of highly stringent, in-house tests conducted on test specimens, our product achieves USCAR test results of between Class 4 and 5 - the two highest classes,” says Dähling.
Flame-retardant and also laser-transparent
Most flame retardants also diminish the laser transparency of thermoplastics, which is why PBT, polyamide 6 and polyamide 66 compounds with good laser-weldability and high flame-retardant properties are rarely seen on the market. They are, however, needed for components in battery systems for electric vehicles.
Dähling: “With Durethan BKV30FN04LT, we can offer a corresponding compound based on polyamide 6. With its halogen-free, flame-retardant package, it passes the UL 94 flammability test of the US Underwriters Laboratories Inc. testing organization for small test specimen thicknesses with the top classification of V-0.” The material can be safely processed within a stable process window and leaves hardly any deposits in the tool. Its high tracking resistance of 600 V (CTI A, Comparative Tracking Index, IEC 60112) makes it ideal in components for high-voltage batteries and plugs.
Tailor-made for greater wall thicknesses
The third new Lanxess material for laser welding is Pocan TP150-002. The 30-percent-glass-fiber-reinforced PBT compound is optimized for extremely high laser transparency. It exhibits a transmission of 13 percent, which is around double the transparency of most other laser-transparent PBT product types (measured with a LPKF TMG-3 at 980 nm and a test specimen thickness of 2 mm). “We have tailor-made the material for the cost-efficient laser welding of components requiring a greater wall thickness for design reasons,” says Dähling.