Sustainable Advanced TPE for Mud Flaps
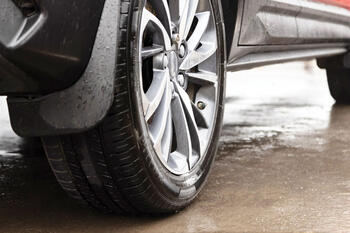
As a major contributor to carbon emissions, the automotive sector is actively incorporating sustainable solutions into manufacturing to achieve its sustainability goals. Even small components like mud flaps and splash guards – designed to protect vehicles from debris, mud, and water while minimizing road noise – are becoming part of this shift toward sustainability.
Kraiburg TPE provides high-quality sustainable TPE compounds with advanced properties to help manufacturers enhance product sustainability while benefiting from cost-effective solutions for vehicle components such as mud flaps, seals, and gaskets. With its versatility and reliability, TPE is an excellent choice for automotive applications, allowing companies to meet both performance and environmental targets efficiently.
A mud flap, also known as a mudguard or splash guard, is typically made of rubber, plastic, or metal. Kraiburg TPE’s advanced TPE materials offer properties that ensure these components perform reliably under all driving conditions. They provide resistance to road debris, grime, weather, and UV exposure while maintaining durability, reducing the need for maintenance for vehicle users.
Kraiburg TPE’s sustainable TPEs provide essential material benefits, including low density for lightweight construction and improved efficiency, thermal stability up to 90°C for reliable performance in high-temperature conditions, and strong weather resistance. These properties make them well-suited for automotive exterior components, ensuring durability against heat, rain, and temperature fluctuations. They also focus on aesthetics, offering high surface quality, a non-sticky feel, and a soft-touch finish to help manufacturers create visually appealing yet user-friendly automotive components. With a range of available shades, manufacturers can also opt for precise colouring and pre-colouring customization.
Kraiburg TPE’s TPEs offer efficient processing in multi-component injection moulding and excellent adhesion to materials such as PP, ASA, PC, PC/ABS, and PMMA. These TPEs also provide strong adhesion to EPDM and TPV, further expanding their application potential. These compounds also comply with multiple global standards, including FDA raw material compliance, RoHS, and REACH SVHC requirements.