Siapi's new strategy: shared know-how and sustainability
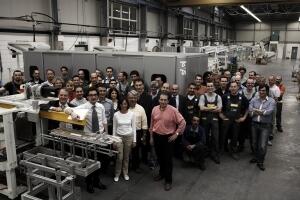
Bespoke design and custom manufacture of blow moulding machines used to make bottles and containers in PET, PP, PLA and other resins is the core business of the Italian company Siapi. In 2013, it launched a new business strategy, namely a more hands-on approach and on-site support in target markets, tangible responses and tailor-made solutions that take into account the evolution of demand not just technologically speaking, but also in environmental terms.
To achieve this mission, the company decided to invest in setting up symposiums and events, which act as vehicles to convey important information on its offer. The last conference was organized in Gammarth (Tunisia) in cooperation with Siapi Africa, and served to present the range of solutions and applications available for the African market, which, in 2013, has become a new force driving the internationalization process of the company. Of particular interest was the afternoon debate, which focused on the pursuit of quality in blow moulding processes for PET bottles and containers. Siapi's top management went over the company's strengths - speed, simplicity and shape - qualities linked to our technological drive, twenty-year background in the industry and our ability to bring any idea to life, tailoring designs and machinery to the customer's requirements.
The next symposium is scheduled for September 2013 and will see SIAPI heading to Mexico, a budding market in this sector. A topic of particular interest was the pursuit of quality in the blow moulding process for PET bottles and containers through strengths such as speed, simplicity and shape linked to the technological drive, the twenty year background and the ability to bring any idea to life, tailoring designs and machinery to the customer's requirements.
Another crucial objective of Siapi is the reduction of the environmental impact. To promote energy savings, the company has now adopted a blow air recovery system, resulting in an average saving of up to 40% compared to traditional solutions. Another step in this direction is the purchase of a line of energy-efficient latest generation ovens, helping keep costs down by optimizing processes and increasing hourly throughput.