New head of sales and business development for Ferromatik Milacron in Europe
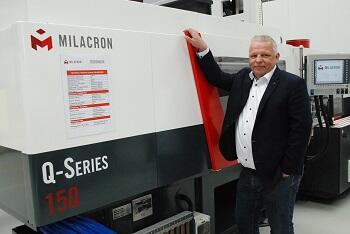
The pan-European full-range supplier of servo-hydraulic and all-electric injection moulding machines, Ferromatik Milacron, announced the appointment of Peter Kochs as Director Sales and Business Development. Peter Kochs, 54 years old, previously held a senior position at Windsor for 12 years.
Michael Jones, President, Milacron Plastics Technologies Group, Cincinnati (USA), underlined this important personnel decision with these words: “We value and appreciate Peter Kochs’ high level of knowledge regarding the plastics industry. His 25 years of profound experience with injection moulding technology defined him as the ideal candidate for this responsible position. We know Peter is committed to resolving present and future customer expectations within the challenging European markets.”
Strengthening sales and market development of the enhanced C-Series, Q-Series and Maxima Performance injection moulding machines as well as the new injection moulding machine launches expected in autumn 2021, including mono-sandwich units. “That's the scope of major challenges for our sales team at Ferromatik Milacron in Teningen (Germany), at the subsidiaries and business/trade partners in Europe”, confirmed Peter Kochs.
"After the consolidation phase accomplished during the last two years, the introduction of new machines combined with a fast and effective service including PDQ accessory parts supply are now at the top of our to-do list - both for the current machine portfolio of servo-hydraulic and all-electric injection moulding machines as well as for the entire fleet of machine generations installed worldwide," explained Winfried Stöcklin, Managing Director of Ferromatik Milacron. "To this end, our dedicated teams offer complete solutions through the life of our products. We also present value-added design that allows machines to be adapted to new applications and to further increase productivity. We will meet the requirements of the target industries with a straightforward number of series and models based on the modular principle."
FME now benefits from the joint know-how - especially marked by the capital-specific backing from Milacron and the unique technological features of Milacron USA and Milacron India. At the Teningen site, FME has around 1000 m² of operating space for application technology, service and support as well as over 900 m² of office space. Here, the company employs a staff of injection moulding experts whose knowledge is based on 65 years of IMM technology and an enormous wealth of experience in design and production: "This is what the company thrives on, integrated in the Milacron group structure. The subsidiaries in France, Spain and the Czech Republic, the location for logistics and warehousing, benefit equally from these advantages," said Kochs.
The activities undertaken in 2019 gave this brand a new identity: R&D and engineering are jointly organized on a global scale (USA, Germany and India). Customer-specific adjustments, commissioning and after-sales service are carried out in Germany or from Germany. The IMMs for Europe are manufactured in accordance with Milacron's global quality standards at the Milacron India plant in Ahmedabad, a state-of-the-art production facility with 30 years of plastics experience and a capacity of 2,500 to 3,000 IMMs (up to 80,000 kN clamping force) per year.
FME has clearly set its compass on positive growth. By the time of the next trade fair - Fakuma 2021 - decisive cornerstones have been set in order to increase the attractiveness of Ferromatik machines, including their non-material values: technology upscaling, AI, M-Powered, Industry 4.0, controls, peripherals, user-friendliness, service network and more: "We are on target with these issues. Our machines are at the most competitive state of the art," confirmed Winfried Stöcklin and Peter Kochs in unison.
Milacron and its parent company, Hillenbrand, are actively involved in building its sustainability program with a focus on its customers. Making sure its products provide strong customer benefits and solve for sustainability needs of the end-user is a focus. This also includes the all-electric eQ-Series injection moulding machines which will be presented on the occasion of Fakuma 2021. In the Monosandwich, the combination of skin and core material gives the parts their special characteristics, allowing for potential material cost reductions of up to 30%. This opens the door for more application to use recycled material in a wider array of products, better serving customer needs.