New shuttle stacker from WM Thermoforming Machines
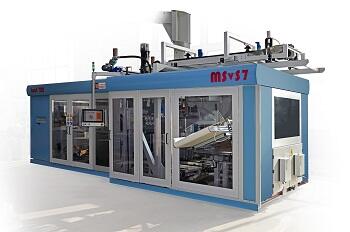
In WM Thermoforming Machines there is a new stacker, freshly patented and previewed at the K 2022 show in a livestream connection with Stabio headquarter. The new MSvS is an evolution of the previous model, the MSv Stacker. The extra “-S” stands for Shuttle and Speed.
“The new MSvS is an evolution of the classic MSv stacker. It includes all of its signature features, such as: easy setting for quick changes (item pick-up position, unloading position, stacking height, catching mandrel height); optimized layout; possibility to stack hard-to-stack products (vertical stacking using gravity plus special evacuation belts plus integrated system for automatic packaging machines); operates at maximum machine speed; tool accessories cost”, Maurizio D’Adda, Head of Technical Department, stated.
MSvS: whats’ new?
The distinguishing feature of the new MSvS is its unique “shuttle system”. In the “previous” MSv the finished pieces were picked from the forming station then transferred into a first basket until it was filled up, then vertically transferred into a second basket placed under the first one. As a matter of facts, the main trait of MSv stacker was the vertical discharge.
“The vertical discharge is a very good solution to avoid the use of gripping notches that can potentially scratch the formed products or deform them, especially when they are still hot and soft. With the MSvS and its unique stacking system the advantages go to the next level: the improved capacity of the stacking basket allows for improved stacking basket capacity for a better handling of the downstream operations; and by eliminating the basket-to-basket transfers a greater process stability is achieved”, D’Adda added.
MSvS: the shuttle system
“MSvS features two separate stacking baskets: one on the right and one on the left side of the machine. Shuttle system refers to the movement of the catching plate, shifting to the left and to the right to pick up and deposit the products at turn in the two stacking cages. The stacking robot starts filling up the first basket. When the first basket has reached the maximum capacity, it starts filling up the second basket on the other side. In the meantime, the first basket discharges the pieces on the conveyor belt, and is ready to be filled up again. The process is fluid and continuous, wasting no time. The shuttle with seven electric axis moves from one side to the other of the thermoformer, to pickup and deposit the finished parts. The accelerations are really impressive”, the technical head continued.
“In addition, we have integrated two additional features: the automatic discharge of the formed parts of a single cycle, for easier quality control; the bridge conveyor with automatic sheet feeding, that feeds automatically the sheet up to the scrap winder with no intervention by the operator. During the K show 2022, MSvS was presented with a livestream preview while it was operational on a Twist 700 running in our headquarter in Stabio. We now invite all the customers to come to WM’s headquarter to take a look Live”, D’Adda concluded.