Precise injection moulding of light components
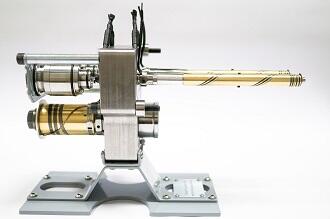
At Molding Expo 2019, which takes place from May 21 to 24 in Stuttgart, HRSflow presented its new small-sized SA series hot runner nozzles for injection moulding small technical components with a very compact cut-out in the tool. The company also showcased extensions of its cylinder portfolio which are particularly compact and require little installation space, including versions developed for exact needle adjustment.
Nozzles
With the new screwed-in hot runner nozzles of the SA series, HRSflow has expanded its range by a size, which is ranked even below the to date smallest P series. They are suitable for the injection moulding of technical parts with a shot weight of about 1 g and less and for wall thicknesses below 1 mm. Their selectable gate versions open nozzle and valve gate are available with bushing through the cavity or gate on the cavity. The shape and material of the tip, the channel section and the contact surface of the end ring with the cavity are designed to have optimal thermal conditions allowing for a high flexibility in processing engineering polymers.
Their typical applications range from the automotive industry to technical components, houseware, logistics and environmental applications including productions with frequent colour changes as well as the processing of glass fibre reinforced plastics or the moulding of parts with particularly high-quality surfaces for subsequent painting or coating processes. The use of stack moulds is possible.
The compact design of the new SA series enables a compact cut-out in the tool. At the same time, the relatively large melt channel diameter allows the processing of highly reinforced or highly viscous plastics at high flow rates. The nozzle screwed on the manifold guarantees the seal at high injection pressure without requiring accuracy in the machining of the mould.
Cylinders
HRSflow's extended cylinder portfolio now includes compact hydraulic cylinders, which require small cut-outs in the tool and provide an increased thermal insulation thanks to components material and optimized contact surfaces. This minimizes the heat transfer to the manifold and reduces energy consumption. Here, in addition to the basic version, a version with needle damping is also available. Further variants offer a micro-switch version for the double needle end position detection as well as an adjustable version offering the possibility of compensating the position of the needle by ±1 mm without mechanical reworking.
Finally, HRScool is HRSflow’s innovative solution for hot runner injection moulding in which the water cooling of the associated actuators can be completely eliminated for the most common automotive applications. Support columns with optimized contact surfaces minimize the heat transfer from the hot tool plate to the cylinder, while a height-adjustable cover plate made of a highly thermally conductive material ensures the maximum heat dissipation from the cylinder to the cold clamping plate. By removing all elements required for active cooling, such as ducts, pipes and connections, HRScool eliminates issues associated with clogged cooling circuits.