Sica belling machines focus on productivity and energy saving
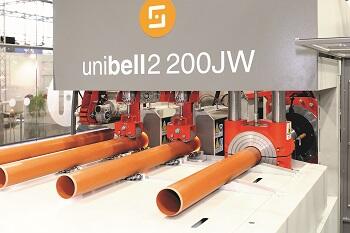
The need for innovative “green” technology in the plastic pipe production industry capable of guaranteeing high performance, process flexibility and ease of use while allowing reduced energy consumption, has become increasingly pressing and has had a marked influence on the design of various types of extrusion line machinery, including belling machines. In order to meet these needs, Sica has “gone green” with a range of machinery geared to saving energy, material and process costs.
Regarding belling machines, an example is the use of short-wave ovens that are active only during the heating phase and for the time needed to reach the final set temperature of the material, thus reducing energy consumption and avoiding scrap material. In addition to this, an electromechanically operated socket forming unit has replaced conventional hydraulic and pneumatic solutions, bringing several benefits: highly dynamic operation, low noise levels, excellent precision and repeatability of positioning, total real-time control of process parameters in terms of working strokes and speeds, and no contaminating fluids. These are important advantages especially for belling machines for small-size pipes that were originally pneumatically operated.
All Sica new belling machines like Unibell and Multibell for PVC pipes, or Everbell for PP pipes, are highly productive (many models process more than one pipe simultaneously) and ensure low energy consumption. As a result, the machines incorporating technologies with a reduced impact on the environment also entail a reduction of production costs, thus allowing faster returns on capital expenditures.