The largest model of the servo hydraulic series
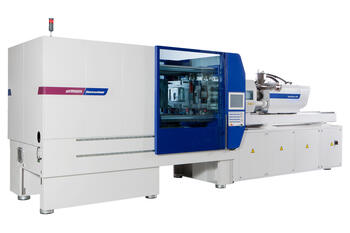
With SmartPower 350, on show at Fakuma trade fair in hall B1, stand 1204, Wittmann Battenfeld has completed its PowerSeries product range with the larger sizes from 160 to 350 tons.
The SmartPower is equipped as standard with an extremely energy-efficient, innovative servo hydraulic drive, which stands out by its high dynamism and low noise level. Moreover, the drive technology of the SmartPower makes it possible to use the KERS (Kinetic Energy Recovery System) developed for the EcoPower. KERS transforms the kinetic energy released by deceleration into electrical energy. The electrical energy recovered in this way is partly stored, used by other drive systems for parallel movements, transferred to barrel heating or used to generate the voltage for the control system. This means that the entire deceleration energy is used within the machine.
The clamping system of the SmartPower comes with a centrally operating cylinder piston. The hydraulic blocks are integrated directly on the clamping side to ensure extremely high control accuracy and dynamic movement sequences. Two symmetrically positioned travelling cylinders provide force transmission with mould protection and fast movements.
In this machine series, injection control is effected via the highly dynamic servo drive. The open design of this machine simplifies its operation and coordination with material feeding and drying equipment.
With the SmartPower, the clamping force range of the hydraulic machine series has been extended from 300 t for the previous model HM to 350 t. The diagonal distance between tie-bars has also been increased. The SmartPower 350 offers generous mould fixing dimensions of 800x720 mm distance between tie-bars, combined with an extremely compact footprint of the machine. The open design of the frame includes an open ejection area in three directions. The installation of conveyor belts for parts removal presents no problems. Another special feature is the easily pivoting injection unit, available up to size 3400. This unit significantly facilitates access to the nozzle and the screw, and consequently servicing of the screw.
At Fakuma, a “natural fibre organic sheet” component is produced with a single-cavity mould from Georg Kaufmann (Switzerland), on a SmartPower 350/2250. The mould is equipped with a hot runner with needle shut-off, an edge folding slider for in-mould forming of the organic sheet and a punching die to punch out an aperture in it. The automation system developed by Wittmann Robot Systeme in Nuremberg is custom-made for this application and comes with a station to feed the organic sheets cut to size, a heating station to heat the organic sheets with heating elements supplied by Krelus (Switzerland), and a multi-functional gripper with a needle gripper to pick up the heated organic sheet, and a suction unit for finished parts removal.