Boosting production during laser plastic welding
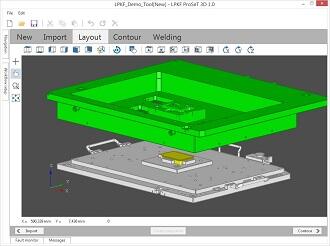
You don’t always need big machines to achieve significant production advances. At Medtec (Stuttgart, April 4-6) LPKF showcased technologies and developments which can give a major boost to productivity and economic efficiency.
The new laser welding systems are supplied with a calibrated working area, Soft-PLC, and the high performance ProSet 3D CAM software. ProSet 3D takes the CAD data for the clamping tool and the product, and uses this to determine optimal welding contours in only a few minutes - even with a fluctuating welding surface in the Z direction. Thanks to the calibrated working area, this data can be extrapolated to all LPKF systems using Soft-PLC - nothing extra is needed to set up the project. The welding system requires no additional setting up, the process parameters generated in this way can be used without any further modification on LPKF laser systems with calibrated working areas.
A premiere at Medtec: LPKF presented a solution for existing welding machines. The WeldPro Light software takes the process data from ProSet 3D, and after a one-off machine calibration, can then transfer the process data without any problems.
Another exhibit was the announced InlineWeld 6200. This system is integrated within the clients’ own production lines. It features a ProfiNet interface, and is fully controlled via the in place MES. The version with the fine-focus laser showcased at Medtec is completely new. This model is designed for extremely fine and precise welds, and can be used to create weld seams with widths between 0.7 and 2.5 mm.
The high quality standards demanded by medical technology meet their match in the TMG 3. As a stand-alone or integration solution, this transmission measuring device determines the absorption values of components in the wavelengths of the welding laser. Thanks to certification by the German National Test Authority (Physikalisch-Technische Bundesanstalt) this measuring device has been issued with a factory calibration certificate since December 2016, and complies with the DIN 9001 specifications for unbroken product monitoring during the manufacturing pro-cess.
A solution for the production of shallow clear-clear welds uses a laser with a wavelength of around 2,000 nm. Welding takes place by very precise focussing on the welding horizon. The PrecisionWeld is a compact welding system for the production of microfluidic components. Thanks to modern laser technology, and a special overpressure clamping system, it can weld transparent microfluidic parts without harming the sensitive channels.