Footwear manufacturing using 3D printing technology
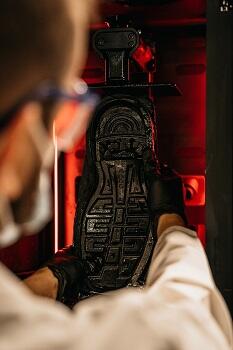
Leader in polymer 3D printing solutions, Stratasys announced that Danish shoe manufacturer Ecco is using Stratasys Origin One 3D printing technology to accelerate product development, allowing conceptual footwear samples to be reviewed early in the development cycle using 3D printed moulds and lasts (mechanical forms shaped like a foot) with resin materials from Henkel Loctite.
Shoemaking is an incredibly manual process, but Ecco has worked to integrate innovative technologies into their shoemaking, allowing for increased automation and a more streamlined development process. One such innovation has been the Direct Injection Process (DIP). This process has given Ecco numerous benefits including an efficient and reliable method of securing the upper part of the shoe to the midsole.
To help further innovate shoemaking and the DIP, Ecco turned to additive manufacturing with the Origin One 3D printer using Stratasys’ proprietary P3 technology. Ecco is using the printers in their Portugal and Denmark development facilities to 3D print moulds and shoe lasts for development purposes that match the quality requirements of their CNC-machined aluminium counterparts. The moulds and lasts, printed from a photopolymer from Henkel Loctite, are faster to produce, and the new process costs significantly less than CNC machining aluminium.
Stratasys partnered with materials providers to test a variety of resins that would meet Ecco’s needs, choosing a formulation from Henkel’s Loctite 3D Printing that was formulated to meet the specific requirements of the DIP process. The combination of Stratasys Origin One 3D printing technology and custom Henkel materials has given Ecco the ability to create shoe moulds that endure thousands of shots with zero visible degradation. Further, the quality of the shoe produced using additive manufacturing technology is on par with those produced using traditional CNC machined aluminium moulds.
By 3D printing the DIP moulds instead of machining them, a single pair of mould inserts can be printed overnight, significantly more cost-efficient than that of an in-house CNC machined pair of moulds. This enables designers and developers to test functional shoes earlier in the development cycle, allowing product teams to confirm the fit and comfort of new styles. Further, branded customers can more easily place real production shoes, in more varieties, in the hands of their potential customers for feedback and pre-sale opportunities earlier in the shoemaking process. Finally, Ecco can now quickly produce mould inserts at the location that needs them, eliminating the need to ship heavy metal moulds, reducing costs, and minimizing the risk of shipping delays or tariffs.
For the wider footwear industry that want to take advantage of 3D printed DIP tooling, Ecco has several flexible routes to market with the ability to assist with every aspect of footwear manufacturing and mould making including engineering, part production, or licensing of IP.