100% electric for PET preforms
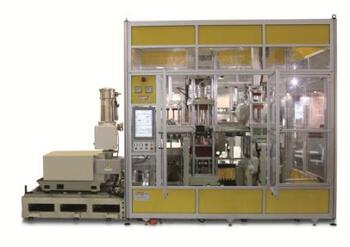
After an absence from the stretch blow moulding market for more than 10 years, Magic MP (Monza, Italy) is back with the BME machine, the first fully electric machine for single-stage processes exhibited at Plast 2015. Marketed as the amalgamation of technology at the service of processors, most prominent among the numerous advantages deriving from its use is energy saving. A conventional small or medium stretch blowmoulding machine with hydraulic drive consumes approximately 25-30 kW (excluding injector) to inject, stretch and blow, while this machine consumes approximately 3 kW to clamp the preforms, the platens (blowing 26-30 Bar) and platen supports as well as the carriages. All the machines are fitted with a single injector model.
Another significant advantage comes from equipment savings. The cost of single-stage machine moulds substantially influences the overal cost of the machine and payback time. Exploiting the new mobile platen system, the machine reduces the blow mould cavities by 50%. The mobile platen system in fact blows the preforms in two stages, saving the cost of the mould and the energy needed for the movements. To get a better understanding, consider that to blow 6 preforms with conventional technology, 6 blow cavities are needed, with a clamping force of approximately 30-35 t. In this case, however, just 3 cavities and a 40% lower clamping force are required.
The versatility reveals another characteristic that distinguishes the new single-stage machine. First and foremost, the absence of cooling system, which with this cycle time is possible because of the speed of electric motors. The cooling system, in any case, can be added at a later time to suit new production needs, by inserting a module into the injection and blowing unit. Lastly, designed specifically for small production runs, the machine blows two bottles of different shapes at the same time, with an apparently similar preform but with different necks.