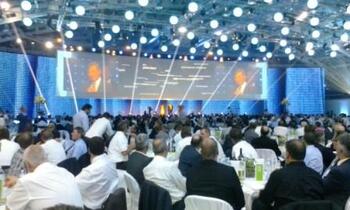
Le presse a iniezione senza colonne (tie-bar-less) di Engel favoriscono libertà di progettazione, lavorazioni efficienti, celle di produzione compatte e idee di sviluppo creative. Periodicamente, il costruttore austriaco premia le applicazioni più innovative su questo tipo di presse con l’Engel HL Award. Il 16 giugno tre società sono state premiate durante l’Engel Symposium, organizzato presso il Design Center di Linz. Gli HL Awards 2015 sono stati assegnati a Hengst Automotive, Gardena e Schneegans.
Per l’ottava volta Engel ha premiato applicazioni che sfruttano in modo eccellente i vantaggi delle sue macchine con unità di chiusura senza colonne e, per la prima volta, i premi sono stati assegnati in tre diverse categorie: “uso efficiente dell’area stampo”; “integrazione di processo innovativa”; “automazione economica”. 27 trasformatori provenienti da 14 paesi si sono candidati per questo premio internazionale. Tutte le applicazioni presentate sono state esaminate da una giuria che, come da tradizione, era composta da tre rappresentanti di università, industria e stampa specializzata: Frank Ehrig, direttore dell’Istituto di ingegneria dei materiali e trasformazione delle materie plastiche (IWK) dell’Università di scienze applicate di Rapperswil (Svizzera), Gunnar Hack, consigliere delegato di Hack Formenbau a Kirchheim Unter Teck (Germania) e Garald Wollstadt, caporedattore della rivista specializzata Plastverarbeiter.
Ottimo utilizzo dell’area stampo
La sostituzione dei metalli con le plastiche sta aumentando rapidamente, coinvolgendo anche componenti che si trovano sotto il cofano motore delle automobili. Hengst SE & Co, con sede a Münster, Germania, ha sviluppato una soluzione termoplastica a base di poliammide rinforzata con fibre di vetro per la produzione di componenti di filtri dell’olio installati in alcuni motori diesel a quattro cilindri di Audi e Volkswagen. Le basi del filtro sono tra i componenti più sofisticati che il trasformatore produce nel suo stabilimento di Nordwalde, Germania. Lo stampo monoimpronta ha, in tutto, otto estrattori, motivo delle sue notevoli dimensioni. La base del filtro viene realizzata con una pressa Engel victory 3550/450 tech, con forza di chiusura di 4500 kN. L’assenza di colonne ha permesso a Hengst di ridurre i costi d’investimento, oltre a quelli operativi per l’applicazione, di mantenere le unità di produzione compatte e di ridurre drasticamente i tempi di montaggio e regolazione dello stampo. Il robot integrato viper 40 può raggiungere l’area stampo direttamente dai lati, senza ostacoli. Questo diminuisce l’altezza di lavoro e assicura che il robot rimanga a debita distanza dalle pesanti gru nell’area di produzione, anche con un soffitto relativamente basso. Per queste soluzioni, quindi, Hengst si è vista assegnare il 2015 Engel HL Award nella categoria “uso efficiente dell’area stampo”.
Un’integrazione innovativa
Con 20 milioni di unità all’anno, i raccordi idraulici per tubi da giardino rappresentano i componenti con il più grande volume di produzione di Gardena Manufacturing, parte del gruppo Husqvarna Group, con sede a Gerstetten, nel sud della Germania. A partire da gennaio 2015, una macchina Engel victory 740H/310W/400WP è stata usata per la produzione di tali articoli e solo l’unità di chiusura senza colonne rende possibile combinare la massima precisione con cicli di produzione molto brevi in seno al nuovo processo a due componenti. Il robot multiasse Engel Easix integrato rimuove 16 raccordi dalla macchina ogni 16 secondi. Per essere in grado di processare contemporaneamente i termoplastici e l’elastomero per la superficie antiscivolo, lo stampo rotante presenta due serie di 16 cavità e quattro serie di 16 nuclei. Il processo si caratterizza per un movimento ingegnoso: dopo che i componenti termoplastici sono stampati, lo stampo ruota i nuclei affinché si trovino in posizione di raffreddamento, prima che avvenga il sovrastampaggio nella terza posizione. Questo evita alla fase di raffreddamento di allungare la durata del ciclo. Quando i connettori si trovano nella quarta posizione possono quindi essere rimossi dallo stampo. Le quattro serie di 16 nuclei sono sistemate in modo lineare. Il cuore dell’unità di chiusura senza colonne, il ripartitore di forze, gioca un ruolo importante per assicurare che i connettori prodotti nelle cavità superiori e inferiori abbiano lo stesso spessore di quelle prodotte nelle cavità centrali. Due di questi elementi centrali flessibili sono situati dietro il piano portastampo mobile e distribuiscono la forza di chiusura equamente sulla sezione trasversale dello stampo. In questo modo, garantiscono livelli di riproducibilità molto alti e un’eccellente protezione allo stampo, contribuendo, quindi, in maniera essenziale all’eliminazione di scarti legati a problemi di qualità. Sebbene lo stampo occupi completamente l’area stampo della macchina con le sue numerose connessioni di raffreddamento, rimane spazio sufficiente per il movimento. l’Engel HL Award 2015 per “integrazione di processo innovativa” è stato quindi assegnato a Gardena.
L’automazione che fa risparmiare spazio
Lo spazio sottocofano di un autoveicolo è molto limitato. Come un grande puzzle tridimensionale, tutti i vari componenti necessari per far funzionare un’auto devono integrarsi con precisione. Un buon esempio è costituito dai moduli di misurazione del livello dell’olio. Per inserirli nel miglior modo possibile nello spazio a disposizione, non sono più realizzati in acciaio, bensì in plastica. Non solo la plastica offre maggiore libertà di progettazione, ma riduce anche il peso del componente, che può altresì essere prodotto tramite processi molto economici. Schneegans Freudenberg Silicon utilizza la tecnologia PIT (Projectile Injection Technology) per produrre oltre 3 milioni di pezzi all’anno per BMW, Daimler, Volkswagen, Seat, Audi e Skoda presso lo stabilimento di Losenstein, in Austria. Ogni 45-50 secondi, due unità interamente assemblate vengono espulse dalla cella di produzione completamente automatizzata, il cui cuore è costituito da una macchina senza colonne victory 400. Quattro robot multiasse integrati condividono il compito di inserire i “proiettili”, rimuovere le parti stampate, distaccare le cavità di traboccamento, stampare gli imbuti sulla parte frontale, inserire gli o-ring, assemblare manicotti e aste di livello dell’olio, verificare la tenuta e imballare i prodotti finiti. Siccome lo spazio è importante sottocofano, ma anche nello stabilimento produttivo di Schneegans, la soluzione senza colonne è risultata ideale per produrre questi componenti. Permette ai robot multiasse di lavorare molto vicino alle unità di chiusura e di accedere alle cavità senza perdere tempo. La tecnologia senza colonne di Engel apporta un contributo essenziale all’elevata efficienza della produzione automatizzata di questo componente, raccogliendo i favori della giuria, che ha conferito il premio al trasformatore nella categoria “automazione economica”.