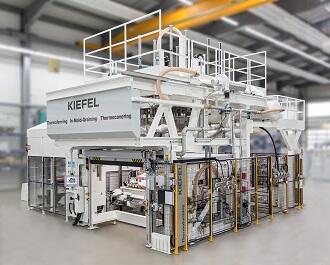
Le automobili moderne non sono solo sempre più sicure, ma presentano anche un design di qualità sempre più elevata. Particolarmente importanti nel condizionare le scelte d’acquisto risultano gli interni, che vengono tenuti in sempre maggiore considerazione. Elementi visivi e tattili utilizzano svariati “trucchi tecnologici” e, dunque, i cruscotti altamente tecnologici con eleganti pannelli strumentazione in pelle artificiale sono sempre più quotati. Il processo di finitura superficiale nello stampo (In Mould Graining, IMG) - nella versione sia di laminato su un substrato sia di una pelle stampata su un retro-espanso - sta divenendo sempre più utilizzata nei veicoli di ultima generazione e consente di ottenere superfici di alta qualità con una struttura omogenea e un buon tocco.
“Dopo un’approfondita ricerca, Kiefel ha saputo raccogliere ancora una volta le istanze attuali e implementarle in due macchine termoformatrici completamene nuove”, ha dichiarato Wolfgang Eglseer, direttore vendite per il settore automobilistico di Kiefel. “Quanto all’area di formatura, le due macchine sono identiche. La differenza consiste nel fatto che una è esplicitamente progettata per lavorare direttamente film da bobina, mentre l’altra crea tranci di materiale partendo da bobine di film, o può lavorare anche tranci preformati”, spiega Eglseer.
Il processo IMG garantisce uniformità alle superfici stampate anche nel caso di componenti distintamente tridimensionali. La finitura superficiale desiderata viene applicata solamente alla superficie in questione durante il processo di termoformatura. Tutti gli azionamenti principali della nuova macchina di termoformatura con vuoto sono mossi da servomotori, che li rendono altamente efficienti dal punto di vista energetico. La tavola inferiore della macchina è azionata da un servomotore ed è orientabile secondo angoli incrementabili di 7,5° fino a un massimo di 90°, assicurando l’ergonomia ideale per l’operatore in considerazione della possibile altezza di ognuno. L’ampia area di formatura consente di produrre contemporaneamente due pannelli strumentazione. “Su tre turni di lavoro la produttività può arrivare a 2000 pannelli al giorno, anche molto alti”, sottolinea Eglseer. La nuova macchina può essere completata con un dispositivo automatico per il cambio rapido dello stampo anche quando la produzione è ancora in corso.