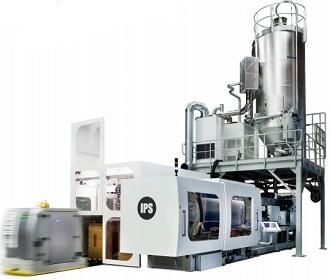
L’innovazione a marchio Sacmi conquista la fiducia di Parmalat (Gruppo Lactalis), che ha scelto la piattaforma IPS (Injection Preform System) per il rinnovamento impiantistico della sede di Piana di Monteverna (Caserta) dove, adesso, vengono prodotte le preforme in PET - tra le più leggere e performanti del mercato italiano - per bottiglie da un litro per latte fresco.
Sviluppata con l’obiettivo preciso di proporre al cliente una piattaforma completa e integrata che si distingua da soluzioni alternative per facilità d’uso, elevate produttività, facilità e rapidità di cambio formato, la macchina IPS 220 si caratterizza per le innovazioni progettuali nell’unità di chiusura stampi, che, grazie a un intenso lavoro progettuale che ha incluso tecniche FEM per l’ottimizzazione delle inerzie meccaniche, garantisce tempi rapidissimi di “lock-to-lock”, riducendo il tempo ciclo di produzione della preforma.
A caratterizzare la soluzione installata da Parmalat è poi
lo stampo a iniezione a 48 cavità, realizzato al 100% da Sacmi sulla base di un’attenta
progettazione interna di ogni singolo componente. Elementi distintivi risultano
i canali ottimizzati all’interno della camera calda, oltre a circuiti di
raffreddamento ad alta efficienza, che agevolano lo scambio termico, ottenendo
così cicli produttivi particolarmente performanti, come dimostrato già in fase
di test durante le simulazioni e validazioni portate avanti in modo congiunto
dal centro ricerche del costruttore imolese insieme al laboratorio ricerca e
sviluppo di Parmalat.
L’impianto fornito a Parmalat non è soltanto una macchina. A incidere in modo decisivo sulla scelta di investimento del gruppo è l’approccio “Sacmi Total Care”, il sistema Sacmi che, grazie alla presenza di avanzati sensori sull’impianto connessi online, consente di monitorare a distanza e in modo predittivo le prestazioni di processo, anticipando le criticità e predisponendo le adeguate soluzioni (come l’invio di ricambi e la soluzione degli aspetti più comuni sulla linea) senza la necessità di inviare in loco un tecnico specializzato. Totalmente integrato e cablato - dalla pressa all’essiccatore, fino ai sistemi di refrigerazione e al compressore - l’impianto può così essere tenuto sotto controllo sia a distanza sia da qualsiasi dispositivo connesso alla rete aziendale, anticipando ogni necessità (approvvigionamento ricambi, interventi di manutenzione) e minimizzando così i fermi produttivi.
Risultato, un modello di produzione intelligente che va nella direzione dell’industria 4.0”, la strategia che - tramite l’ausilio della sensoristica avanzata e delle nuove tecnologie - si traduce in un approccio innovativo al prodotto e al servizio, restituendo un nuovo orizzonte di riferimento per la migliore manifattura italiana.