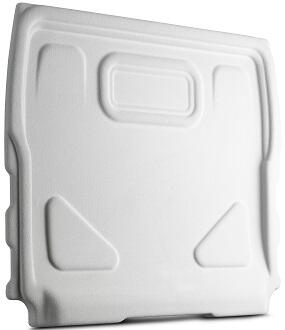
A JEC World 2019 Sabic ha annunciato la produzione di pannelli per veicoli leggeri, economici e riciclabili con l’impiego del nastro Udmax, realizzato in composito termoplastico unidirezionale rinforzato con fibra. Questa nuova tecnica di produzione, studiata per sostituire i pannelli tradizionali in metallo e termoindurente negli interni e negli esterni auto, verrà presto impiegata per realizzare su vasta scala una paratia per veicoli commerciali leggeri (LCV), esposta proprio in occasione delle fiera parigina dedicata ai compositi. La paratia è il frutto di uno sviluppo congiunto internazionale che ha coinvolto Sabic, RLE International, fornitore britannico di servizi di ingegneria, AMA Composites, costruttore italiano di attrezzature, e Setex Textil, produttore tedesco di tessuti.
I pannelli per veicoli realizzati con nastro Udmax uniscono robustezza, resistenza all’urto e leggerezza e possono ridurre dal 35 al 50% (nel caso dei pannelli esterni) la massa rispetto ai componenti in metallo. I pannelli vengono prodotti attraverso un processo ad alta efficienza che prevede la laminazione monofase e lo stampaggio a bassa pressione.
L’uso di compositi termoplastici può permettere significative riduzioni della massa delle applicazioni. Nel caso della paratia, la sostituzione del componente in metallo con un laminato a base di nastro Udmax ha consentito di ridurre del 35% la massa del componente, la cui movimentazione risulta così più agevole a tutto vantaggio dei tempi di assemblaggio del veicolo.
La riduzione della massa può essere ottenuta senza compromettere le prestazioni di resistenza all’urto del componente, caratteristica essenziale per proteggere i passeggeri dagli infortuni derivanti dallo spostamento dei carichi. La paratia è conforme allo standard ISO 27956 per la sicurezza del carico nei veicoli commerciali leggeri. La resistenza alla trazione del nastro Udmax e il processo di lavorazione sono i principali fattori per ottimizzare la resistenza all’urto della paratia.
Rispetto a un componente metallico o stampato a iniezione di una paratia convenzionale multi-pezzo, la nuova tecnica, studiata, sviluppata e ingegnerizzata da RLE International, può ridurre i costi delle attrezzature fino all’80% rispetto a quelle necessarie per lo stampaggio a iniezione. Questo risparmio è possibile grazie al materiale che consente di sostituire uno stampo costoso, ad alta pressione, con uno stampo più economico, a bassa pressione. Complessivamente, il costo di fornitura della paratia per veicoli commerciali leggeri può essere ridotto del 10% rispetto a quello della paratia in metallo che va a sostituire.
Questa tecnica migliora l’efficienza e riduce la complessità della produzione di pannelli per veicoli. Con tempi di ciclo di stampaggio inferiori a due minuti, il processo risulta più snello ed evita l’acquisto e l’assemblaggio di molteplici componenti, provenienti normalmente da più fonti di fornitura, come pure le operazioni secondarie di verniciatura e rifilatura.
La laminazione basata su un nastro Udmax extra largo, tessuto da Setex Textil, incorpora una superficie estetica, ottenuta con una singola fase di compressione. Il processo permette anche di cambiare lo spessore del pannello, per migliorare i livelli di rumorosità, vibrazione e durezza (NHV), contribuendo a migliorare la silenziosità del veicolo. AMA Composites ha realizzato a tale scopo un apposito stampo e stampato i pezzi concettuali.