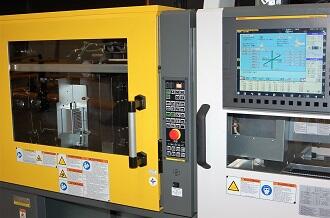
Una open house per dare ampio spazio alle tecnologie per lo stampaggio a iniezione elettrico si è svolta il 26 novembre presso la sede di Fanuc Italia a Lainate (Milano), dove era in funzione una macchine Roboshot α-S100Ia, dotata di robot sviluppato in collaborazione con TecnoMatic di Osimo (Ancona).
Le presse Roboshot utilizzano la tecnologia di precisione CNC mutuata dalle macchine per tornitura e fresatura, così da ottenere maggiore accelerazione, elevata precisione di movimento e tempi ciclo estremamente brevi per produrre grandi quantità di componenti di qualità e con la massima ripetibilità. Tale gamma comprende diversi modelli con forza di chiusura da 150 a 4.500 kN e tutti i modelli iA per lo stampaggio a iniezione elettrico si caratterizzano per estrema precisione e affidabilità, per migliorare la produttività e ridurre i costi di produzione. Per assecondare le esigenze di settori applicativi specifici, di recente sono stati introdotti modelli come l’α-S150iA “Medical Package” per la produzione di articoli medicali (certificato per l’utilizzo in camera bianca ISO 7) e l’α-S50iA “LSR Edition” per la lavorazione dei siliconi liquidi.
I modelli Roboshot condividono con i robot Fanuc stessi ambiente e interfaccia e il pacchetto QSSR (Quick and Simple Start-up of Robotization) semplifica il collegamento dei robot antropomorfi alle presse: l’impostazione dei parametri risulta agevolato e la messa in servizio della cella viene attivata in pochi istanti, rendendo l’operatività di fatto immediata. Per il carico/scarico efficiente della pressa, Fanuc offre la possibilità di integrare un robot cartesiano controllato da sistema CNC Power Motion i-A. Questa soluzione di automazione evidenzia i vantaggi dell’approccio “One Fanuc” e di Fanuc come interlocutore unico per quanto riguarda l’elettronica dell’intera soluzione e il controllo del processo.
La gamma Roboshot è “Industry 4.0 ready”, conforme allo standard Euromap 77 che abilita il collegamento delle macchine in rete e l’interfacciamento con i sistemi MES attraverso il protocollo OPC UA. Tutte le presse integrano nel CNC Roboshot-LINKi, il software che attiva il monitoraggio delle presse in tempo reale da PC remoti e dispositivi smart, fornendo l’accesso a una serie di informazioni relative a produttività, qualità, tracciabilità e diagnostica avanzata, per un controllo totale in chiave 4.0. LINKi permette di visualizzare in qualsiasi momento tempi di attrezzaggio, di avviamento, di produzione, avanzamento dei processi, allarmi e fermi macchina, cicli di produzione, impronte attive ecc. per intraprendere in modo rapido e tempestivo le necessarie azioni correttive, senza interrompere la produzione.
Roboshot monta il CNC Fasnuc 31-iB, completo di funzionalità avanzate di intelligenza artificiale per la protezione degli stampi. Tra queste, AI Mould Protection e AI Ejector Protection misurano la coppia del motore e arrestano immediatamente la macchina se si verifica un problema. La stessa tecnologia consente di proteggere il movimento in avanti dell‘estrattore e quello inverso. Diversamente dalla protezione sui sistemi idraulici, la funzionalità di protezione dello stampo non ha alcun impatto sulla velocità di chiusura. Questo tipo di reattività a velocità elevata è fornita dagli azionamenti elettrici. Anche le tolleranze dell‘unità di apertura e chiusura stampo sono programmabili per l‘intero movimento dello stampo.
Clamp Force Adjustment è una funzione che consente di controllare e regolare automaticamente la forza di chiusura minima, garantendo in tal modo maggiore sicurezza ed eliminando la necessità di regolazioni manuali. In questo modo si riducono l’usura dello stampo, i difetti delle parti e i tempi di avviamento e si estende la durata delle macchine, a fronte di un minor consumo energetico.
AI Metering Control attiva il controllo intelligente per evitare flusso di volume non controllato tra il termine della plastificazione e la decompressione. Questa funzione consente di eseguire in modo automatico il controllo della decompressione avanzato con rotazione inversa della vite dopo la plastificazione e di verificare il volume dopo la regolazione della plastificazione, il passaggio da controllo di velocità a controllo di pressione automatico e la decompressione. Tra i vantaggi: volume di plastificazione costante per materiali a bassa viscosità, riduzione delle variazioni di peso delle parti, possibilità di evitare bolle e altri difetti e qualità delle parti più elevate, con minori scarti.