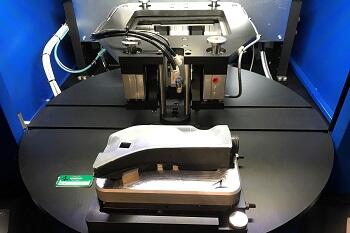
Azienda del gruppo Think Plastic, realtà attiva nel settore della trasformazione delle materie plastiche, Werkcam, con sede ad Arcore (Monza Brianza), è nata per produrre componenti per gli aspirapolvere Vorwerk Folletto. Dal materiale plastico al prodotto finito, Werkcam segue tutte le fasi che portano alla realizzazione dei suoi manufatti: progettazione, prototipazione, collaudo e produzione in serie. Il risultato finale è una gamma di prodotti finiti che uniscono prestazioni ed estetica, caratteristiche imprescindibili nel mercato degli elettrodomestici di alta gamma.
Proprio la necessità di ottenere elementi in grado di garantire il perfetto funzionamento dell’elettrodomestico e allo stesso tempo un aspetto gradevole ha spinto Werkcam a ricercare una soluzione innovativa per la realizzazione di un serbatoio di acqua e detersivo per una macchina lavapavimenti. Il serbatoio risulta a vista, il che spiega l’importanza dell’aspetto estetico; la struttura del prodotto impone inoltre una perfetta tenuta delle saldature per evitare perdite che potrebbero compromettere non solo la qualità della pulizia delle superfici, ma il funzionamento dell’intera macchina. In pratica, Werkcam si è trovata a ricercare una soluzione che garantisse la stessa perfetta tenuta e la totale assenza di sbavature di un prodotto realizzato in un unico blocco, sebbene le caratteristiche progettuali imponessero la realizzazione del serbatoio mediante l’unione di due mezzi gusci in polipropilene.
La scelta della tecnologia da utilizzare a questo scopo è caduta sulla saldatura laser, per gli ottimi risultati ottenuti in campo automobilistico e medicale, e in particolare sulle saldatrici di Leister Laser Plastic Welding, divisione di Leister, costruttrice di sistemi per la saldatura e la lavorazione di manufatti in plastica, che si occupa esclusivamente di tecnologia laser.
I due mezzi gusci in polipropilene vengono saldati in una cella robotica, dove il primo mezzo guscio, trasparente, è attraversato dal laser che viene “fermato” dall’altro mezzo guscio, realizzato con uno speciale additivo in modo da assorbire l’energia del raggio laser. L’accurato apporto di energia reso possibile dall’apparecchiatura permette di fondere l’esatta quantità di materiale plastico necessaria a creare una saldatura resistente, a tenuta perfettamente stagna, senza alcuna sbavatura e in tempi rapidissimi. Un robot antropomorfo sposta il serbatoio saldato verso la stazione di raffreddamento, che avviene molto rapidamente, anche perché, grazie alla precisione della tecnologia laser, le parti non si riscaldano più del dovuto durante la saldatura. Segue il collaudo della tenuta, al termine del quale il serbatoio è sottoposto a marcatura laser per consentire una perfetta tracciabilità di ogni componente del prodotto finito.
Fra i sistemi per la saldatura laser della plastica di Leister, è stato scelto Novolas WS-AT, soluzione chiavi in mano facile da integrare nei processi produttivi. Modulare e versatile, è disponibile con espansioni e accessori collegabili con facilità, come una tavola rotante per l’indicizzazione e un nastro trasportatore. Gli accessori disponibili hanno permesso di adattare il sistema alle esigenze di questa particolare applicazione. Il software di controllo permette di variare con facilità i parametri di saldatura, accelerando le operazioni di sintonia fine per il raggiungimento della saldatura perfetta. Il software comprende il monitoraggio in linea per identificare immediatamente eventuali anomalie durante la lavorazione.