Polyamides for electric concept car
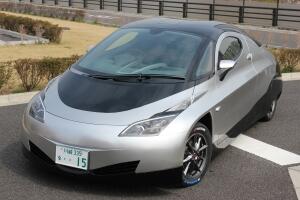
The latest prototype car from SIM-Drive Corporation, a pioneering electric vehicle developer in Japan, features DSM's Stanyl and EcoPaXX based parts that make the car lighter and more sustainable. The Sim-Cel is the third prototype of an advanced all-electric car incorporating in-wheel motors that the company has developed since it was founded in 2009.
SIM stands for Shimizu In-wheel Motor, and CEL stands for Cool Energy Link. Shimizu says that society has until now relied largely on fossil fuels and nuclear power for its energy. "The new energy cycle proposed by SIM-Drive will be able to effectively utilize renewable energy that does not emit excess heat," he said at the unveiling of the new car.
SIM-Drive Corporation aims to ensure the widespread usage of electric vehicles. Development of the SIM-CEL, which took around one year, involved close collaboration with 26 outside organizations, including DSM. DSM personnel were located at SIM-Drive's development center on a full-time basis, and were actively involved in the prototyping process.
The SIM-CEL prototype focuses on high performance, while also using energy smartly to passenger comfort. It has a range of almost 325 km on a single charge, and it can accelerate from 0 to 100km/h in just 4.2 s. This outstanding performance is in part due to lightweighting technologies developed in collaboration with DSM and Others.
DSM contributed to the development of three parts for the SIM-CEL: a body panel in its EcoPaXX polyamide 410; a wheel cover center cap in the same material; and a heat sink for highly energy-efficient LED headlights in Stanyl TC polyamide 46. EcoPaXX polyamide 410 is 70% resourced from the castor plant. It is certified 100% carbon neutral from cradle to gate.
Kees Tintel, who was responsible for development of EcoPaXX at DSM, says the new grade contributes to weight reduction in the SIM-CEL by replacing metal; the part is in fact at least 50% lighter than a metal version. EcoPaXXs very good flow properties provide an excellent surface finish, and it has the necessary high temperature resistance to enable inline painting along with the rest of the vehicle. Unlike some other polyamides, it absorbs little water, and therefor has a very good dimensional stability. It also has sufficient elasticity to enable assembly with snap fits.
In order to improve overall aerodynamics, the SIM-CEL incorporates spats, or fender skirts, which cover the rear wheel arches. These are also made in DSM's EcoPaXX polyamide 410, further contributing to the sustainability of the car, its low weight and its good aesthetics.
The SIM-CEL uses LED's in its headlights in order to use as little electricity as possible. For the heatsinks of the LEDs, DSM developed a special thermally conductive grade of its high temperature resistant Stanyl TC polyamide 46. Stanyl TC551 has a surface thermal conductivity of 14 W/mK and a volume thermal conductivity of 2.1 W/mK.