The importance of tests
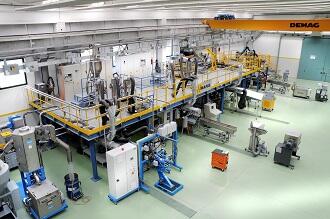
As with a boxer, who needs to constantly train very hard to beat his opponents, technologists need to do exactly the same to knock down the limits set by the market laws. In the sectors of synthetic materials and biomaterials, for example, these limits are periodically overcome by new products, which are tested in a laboratory first, and then made available to the market and distributed, improving quality of life.
Funnily enough, behind these incredible material evolution, there is just one machine: the corotating twin screw extruder, an efficient dynamic continuous mixer, flexible and adaptable to different types of processes, ensuring continuous material feeding. Of course, with the aim of keeping pace with the constant evolution of the market, it is necessary to have business intelligence and flexibility, moving fast so as to quickly offer new solutions for the problems arising day-by-day.
The Technological Center
As it happens with a boxer, who cannot imagine getting on the ring without training, in the same way, an extruder manufacturer cannot place equipment on the market without testing its performances on the different applications. That is why Maris has created its own “gym”, the place where it trains to solve process problems together with its customers, testing their own materials: Maris Technological Center, an R&D department divided into two areas, the Testing Area and the Characterization Laboratory.
The Testing Area, besides being the company showroom, is the heart of the R&D process. Here, there are four complete extrusion lines: two laboratory-scale lines (models TM 20HT and TM30HF) and two production-scale lines (models TM41HS and TM 58HF), permanently installed and at full disposal of the company staff to allow the correct setting of the complete lines for each type of process. In addition, Maris extrusion lines include all the upstream and downstream auxiliary devices, to permit the exact simulation of the most different extrusion processes.
The Characterization Laboratory allows real-time checking
of the properties of the materials produced in the Testing Area. Such features,
compared with a reference sample supplied by the customer, allow discriminating
the effects of the different process variables on material quality, providing
the Testing Area with guidelines to continue the compounding tests.
How does the work at the Technological Center originate and develop?
It all starts from the need of a customer, who asks the company to test their formulations in the technological laboratory. The technicians discuss any possible problem linked to material feeding or to the process (thermal profile, screw profile, filling grade of the screw), then start carrying out the tests on the pilot plant (TM 20HT and TM30HF) with small amounts of materials, in order to produce a sufficient number of samples.
The Characterization Laboratory analyses the products using internal methods, specially designed to be quick and similar to those used at the time of production, in order to obtain a very rapid response on material quality. At the end of the tests, the customer supplies the relevant quality data for cross analysis, which should confirm the results of the analysis carried out in the centre. In this way, the company can define the conditions to carry out tests on industrial productions by means of higher size extruders (TM41HS and TM 58HF). This passage is fundament to produce a large quantity of material to be tested by the customer but also to provide suitable information for the scale-up phase, so that the machine is effectively tailored to the customer and its requirements.
“Extrusion Time”
A strong focus on technological development is behind the company’s decision to offer “Extrusion Time”, an assisted rental of the laboratory extruder, a TM20HT, available to everybody, but intended in particular for research centres and universities, to which convenient rates are granted. Thanks to this machine, it is not only possible to produce little quantities of common materials as compounds or masterbatches, but also adhesives. Furthermore, the machine can be used for reactive extrusion, recycling of vulcanized elastomers, polymerization and to try to produce in a continuous way what is normally produced in batches.
Customers who apply for “Extrusion Time”, have the possibility to use, always assisted by the company staff, the Characterization Laboratory for mechanical, rheological, morphological and optical investigations (in the centre there is a small injection press, which allows the printing of samples).
Rubber devulcanization
In order to give its contribution to environmental safety, Maris has developed a vulcanized rubber recycling process, which produces a plastic material that could be re-entered in the production process of new products. After many laboratory and industrial tests, a machinery has been fine-tuned in a way that, by just modifying the process variables, it permits to obtain plastic material for different types of elastomers, such as NR, IR, EPDM, SBR, FKM, NBR, butyl rubber, silicone, and acrylic, which come from technical items, tires, production and post-production scraps. Several plants are already operating worldwide.