The use of plastics in innovative automotive design on the rise
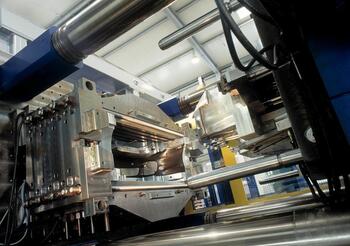
Injection moulding of plastics is continuing its dominance within the processing of polymers to manufacture products for everyday use, including kitchenware, toys and packaging, amongst other end-use industries, according to the new report “Injection Moulding: Global Markets and Technologies Through 2023” from BCC Research.
In 2017, the global market for plastics injection moulding was valued at 117 billion dollars and is expected to reach 233 billion dollars in 2023, reflecting a Compound Annual Growth Rate (CAGR) of 10.9%, as indicated in the BCC’s report.
The thermoplastic polymer segment is expected to witness substantial growth through 2023, owing to the rising demand for plastics across several vertical industries such as packaging and food and beverages. Increasing urbanization, growing income and rising demand from end-use segments further propel the market forward.
More in detail, global demand for polystyrene thermoplastics is expected to increase at higher growth rates over the next few years, due to the increasing popularity of recycled expanded polystyrene products, which has helped the market recover from the setbacks posed by disposal.
The medical device segment accounts for 18.7% of the plastics injection moulding market and is expected to see strong growth over the forecast period as healthcare becomes an increasingly integral part of household expenditures, especially in more developed countries with aging populations.
The Asia-Pacific region will be the largest market geographically, accounting for 35.3% of the global market.
“As the market for injection moulding of plastics continues to grow, so will innovations in resin selection, injection moulding machinery and processing guidelines”, said Christopher Maara, BCC Research analyst and the author of the mentioned report. “With the emergence of new resins with improved properties, moulders can process polymers to fabricate new designs with different properties. Furthermore, with stronger plastics and ease of processing, thermoplastics can save production time and energy compared with making parts from metals”.
Innovations in plastic vehicle interiors are expected to continuously emerge in upcoming years, including advancements such as smart surfaces and 3D-printed tooling, as well as external autonomous driving sensors. Some manufacturers today are even beginning to explore the possibilities of building large portions of the chassis, or the entire chassis, using plastic moulding. The efficiencies and possibilities of such a change, especially as safety improvements, loom closer on the horizon, presenting an exciting development for manufacturers, entrepreneurs and consumers alike.