Multilayer pipes: the first line in the Middle East
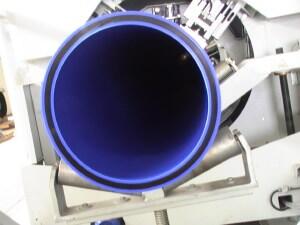
The first multilayer pipe manufacturing line in the Middle East using innovative technology was recently supplied by Tecnomatic. It is a solution capable of reaching output rates up to 2,000 kg/hour to produce PE 100 pipes with maximum diameters of 1,200 mm. Muna Noor - this is the name of the client company which operates in Oman and is part of the Kuwaiti group Boubyan Petrochemical - specialises in the production of PE pipes with diameters of up to 800 mm and recently opened a new plant in Sohar, where it has started producing double-wall PP pipes with diameters of up to 1,200 mm, pipe fittings, inspection holes and ultra-strong multilayer PE pipes. The Omani processor has thus broadened the range of its products, which it also produces under licence on behalf of the Dutch company, Wavin Overseas. Borouge, with its BorSafe HE3490 - LS - H HSCR PE100, was the perfect partner for the supply of raw materials for this project.
The line is equipped with three extruders from the Vega series (L/D ratio = 37), two 60-mm ones for the inner and outer layers, and one 90-mm extruder for the middle layer, which together reach a total output rate of 2,000 kg/hour and guarantee excellent homogenisation of the material. They feature low power consumption, thanks to the design of the optimised plasticisation screw and the AC motors. The line is also equipped with a grooved feeding nozzle, which contributes to the excellent production capacity, an industrial PC with energy consumption analysis modules to control the extrusion process, and remote assistance service.
The new Venus Multi 3 1200 extrusion head, with three spirals, was considered the ideal solution for the extrusion of multilayer pipes using HSCR materials, since it guarantees optimal flow of the melt and optimal distribution of the layers. The head is characterised by compact size, low working pressure (resulting in energy savings) and HCS temperature control system, allowing perfect uniformity of the interior temperature.
It is possible to obtain diameters ranging from 250 to 1,200 mm, three for each die up to 800 mm, by means of the classic draw-down method. For sizes greater than 800 mm, it is preferable to use the "one to one" swelling method, to ensure better control of the eccentricity and ovalisation of the pipe. The mandrels are composed of two parts, with the front part defining the pipe size and the thickness changeover speed. The head is equipped with a solid support carriage with hydraulic tilt for easier dismantling, and a PAC (Pipe Air Cooling) system that provides intense cooling of the inner surface of the pipe, drawing in air in the direction opposite to that of the extrusion process. The air flow ensures even, 360° cooling of the inner surface of the pipe, reducing any variations in its solidification, inner tension and ovalisation and eccentricity, as well as reducing the length of the cooling section.
Every extruder is equipped with gravimetric blenders, to ensure continuous and constant feeding of the material, record flow rate variations, ensure perfect control of the weight per metre, and improve the distribution of the thickness. The blending system is connected with a 16-sensor ultrasonic measuring device, which allows perfect compliance with the process parameters and monitoring of the data relating to the thickness, the inner and outer diameter and the ovalisation and eccentricity of the pipe.
The line includes two calibration tanks: the first (10 m long) can be divided, in the first vacuum section, by means of an electrohydraulic gear, to facilitate the start-up and monitoring of the pipe; the second (8 m), with a single vacuum section, is necessary to ensure the performance of the plant, which requires a longer vacuum section and spray cooling tanks, amounting to a total length of 50 metres. The downstream equipment includes a ten-track haul-off, in which each haul-off is controlled by an independent AC vector motor, and a planetary cutting machine, with blade cutting and universal locking system to ensure accurate processing without burrs.