LSR: injection moulding without a barrel
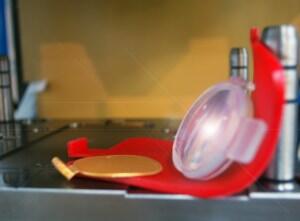
Nowadays, it is getting harder to find true technological innovations during an exhibition dedicated to the plastics and rubber industry. The one reported here - introduced by Guzzini Engineering for the first time at the K Show in Düsseldorf - represents an exception.
On a standard vertical injection machine for thermoplastics processing, the company (a commercial division of Acrilux, one of the companies belonging to the Guzzini family) demonstrated the operation of a revolutionary system for the injection moulding of liquid silicone rubber: EasyBalance Moulding System LSR.
EBM LSR comes from years of experience in the processing of LSR, with the aim of solving the following problems: balancing between cavities, repeatability and precision. So, in short, the advantages of this system are:
- contemporary moulding - in the same mould - of a certain number of products with different weight, thickness and colour
- perfect balancing amongst cavities regardless of their number or arrangement
- strict process repeatability
- it is possible to process silicones with different SH hardness
- reduction of about 50% of cleaning waste
- multi-colour moulding with only one pump.
Furthermore, the system does not require the use of the injection unit of the moulding machine. In fact, it can be fed also by a low pressure feeding system. This makes possible, for example, the moulding of LSR on a thermoplastics injection moulding machine.
The system is able to dose in volumetric mode and transfer into the cavity the amount of material exactly required in the production of the part. This is done through a series of dosing tanks. Both the filling and the emptying of the dosing tank takes place following a FIFO (First in First out) logic: in practice the first material that enter the tank is the first to be injected; this decrease to the minimum the permanence of the material inside the tank and reduce the risk of degradation or vulcanization. Each dosing tank is connected to a low-pressure feeding system and to a masterbatch feeding system. This way every single cavity/part may have a different colour from the others.
So EBM LSR can adapt to changes in production requirements by decreasing the number of cavities to be fed and managing required material volumes even setting different volumes for each cavity, with a precision of 0.1 cc. The latter is particularly advantageous in the production components for the medical industry.