Italian simplicity
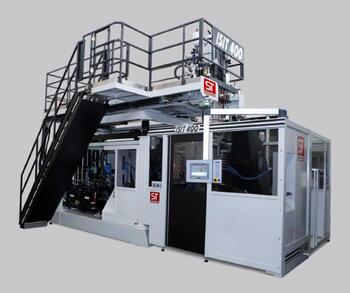
Always careful about market demands, ST Soffiaggio Tecnica will participate in the international trade fair Plast 2015 (Milan, May 5-9), exhibiting its products at stand B 122, hall 22. The company will display the blow moulding machine model Isit 400, part of the latest range of machines that have been added to the more traditional Aspi and TA series. The acronym ISIT identifies this machines series with accumulator head and summarize in one word the identifying feature of the range: Italian simplicity. It is in fact composed of the transcription of the pronunciation in Italian of “easy” (ISI) and the abbreviation of Italian (IT). The technology, ensured by the name of ST Soffiaggio Tecnica, was precisely simplified without sacrificing a high technological level. The Isit series in fact guarantees high productivity with high-energy savings at a competitive market price. Specially developed for the production of blown articles for the technical, automotive and industrial packaging fields, at Plast 2015 the blow moulding machine Isit 400 will be made up of an HEX 60 extruder and an 8-litre accumulator head. The frame, designed to be free from vibrations, is divided into two bases, an upper one for the extruder and the accumulator head and a lower one for the clamping and blowing unit. The upper frame is mobile and electrically adjustable in three directions such as vertical, horizontal and transverse with positions control through magnetostrictive transducers. The more evident innovations are in the clamping unit and in the extrusion section. Regarding the clamping unit, two diagonal guiding columns support and makes the mould platens sliding. In this way, the gripping and extraction pliers of the blown product finds no obstacle, even in the case in which the piece and the associated mould are higher than the platens. The clamping unit is based on three plates, one for the support of each half mould and the third one on which is installed the only hydraulic cylinder that moves the other two. The clamping force is applied to the rear of the plates by means of a crossbar of flexion, which prevents the not balanced transmission forces and any type of deformation. A rack synchronization system completes the clamping unit, allowing a simultaneous and synchronized movement of the mould platens that slide on prismatic guides with roller bearings. The other strength is made by the single-screw extruder which is based on HEX technology (High output EXtrusion) and has a high capacity and plasticizing quality with a significant energy saving, thanks to the special profile of the screw and to the high isolation degree of the cylinder. Therefore, using smaller screw diameters, you can achieve high output of plasticized material, allowing reducing the power used. A heating system with electric heater bands allows transferring the heat to the material in an optimal manner. The heater bands are insulated to avoid heat loss in the environment and the screw does not overheat the material even when it rotates at maximum speed. The lack of cooling fans and the optimal control of the melt temperature allow a considerable reduction of energy consumption. A dedicated software, using an inverter, monitors the pressure and flow of the pump. This ensures greater silence and significant energy saving. The accumulator head with two cardioids is of FIFO type (First In First Out) and is equipped with diverter that ensures a balanced structure and layering of the parison. A linear transducer controls the amount of accumulated material while the extrusion speed and the thickness variation are adjustable in 500 points, ensuring high quality of the produced piece. The blowing unit has a structure connected to the main frame by a roller rail system. This solution allows being able to move it under a half of the mould during the mould change and adjust the position of the blow pin quickly and accurately. The vertical movement is motorized and controlled by a linear transducer and the position can be stored. A reinforcement column closes the unit so that it can also be used with the inclined pin. The extraction pliers of the blown item, electrically driven, is height adjustable to vary the distance between the gripping points and the head, to minimize waste production. Once arrived in the gripping position, a jet of air cools the scrap between the mould and the gripping points, so as to avoid that it "tears" during the extraction phase. In addition to the model Isit 400 on display, the range of ISIT blow moulding machines includes the 500, 800, 1300 and 1600 models.