Five "pillars" for an ever more efficient welding
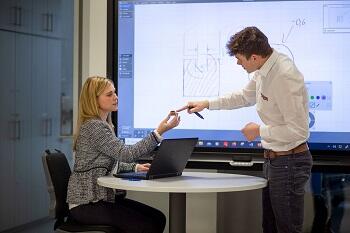
The structure of Hermann Ultraschall services has been optimized under the umbrella term “Herrmann Engineering”. Every single step, from the initial contact with the customer to delivery and start-up of the complete system, is secondary to achieving the best weld results. The ultrasonic specialists can provide a unique combination of services.
A product which suits the customer requirements perfectly doesn’t just appear by chance. Herrmann Ultraschall has systematically examined its business structure and defined five pillars which help to understand the needs of the customers, and to fulfill these needs perfectly. As well as trust, technical expertise, a modular product kit and a global organization, the realization of sustainable solutions is also a central focus.
Herrmann Ultraschall CEO Thomas Herrmann explains: “A relationship between the customer and Herrmann Ultraschall which is based on trust is the basis of everything we do. Our aim is to be viewed as a trusted advisor. This is the only way that the customer can confidently share the sensitive information with us that we need to understand their requirements exactly. This creates communication at eye level. We also share our extensive ultrasonics expertise from thousands of successful projects in training courses and consulting.”
Once the customer requirements have been established, the project management begins. Herrmann Ultraschall calls this phase application engineering. To develop the weld process which is perfectly adapted to suit the specific project, all the relevant aspects are considered, starting from the consulting process for the perfect joint design, to manufacturing the sample parts, right up to the start-up of the complete system and training of the employees.
The project is only complete once the company has done what is possible. Herrmann sums this claim up with the phrase “perfect product”. A big help here is the extensive, modular product kit, which contains the right combination to solve almost every challenge. In the shortest possible time, weld systems are created which can be integrated seamlessly into existing production environments and which provide long-lasting performance during operation. All machines and systems are manufactured in Germany.
Once the weld systems are operational, Herrmann Ultraschall continues to support its customers. Under the motto “global service”, specialists in over 40 ultrasonic laboratories and Tech-Centers in 20 countries are ready to promptly help and advise you in your own language. They regularly perform customer service tasks and inform customers of new trends and options.
The ultrasonic technology is also especially sparing with resources. The process requires less energy than alternative methods and is also more stable. Weld results which can be reproduced in detail ensure that very little material is wasted. Less material is required also for the weld joint itself than in other joining processes. In this way, Herrmann Ultraschall is helping companies to manufacture their products with low energy and material consumption and offer more sustainable solutions to their customers. In the company’s high-tech laboratories, research is also being carried out into the solutions of tomorrow, such as the use of recycled or biodegradable materials.
CEO Thomas Herrmann explains: “At Herrmann Ultraschall, innovation has been a part of the company’s self-image since it was founded over 60 years ago. We have grown rapidly in recent years. The employees are united by an enthusiasm for the ultrasonic weld technology which they can use in their everyday work. We have therefore been focusing on our company culture for quite some time and have clearly formulated our values so that everyone can understand them. We will continue to travel down this road.”