"Green" cutting and belling machines
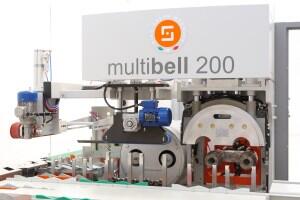
The environment-friendly cutting machine and two belling machines unveiled by Sica at K 2013 are specifically designed and built to save energy and materials and to cut costs. The launch of these machines underlines this manufacturer's increasing tendency to focus not only on the operation and productivity of its machines, and on providing quality at a fair price, but also on reducing the environmental impact of its machines, also ensuring that they allow savings in terms of energy and materials: in short, to focus on economic considerations and sustainable development.
The TRS 160 W cutting machine for PVC, PP and PE pipes is presented as a solution to the problem of dust and chips. Thanks to a patented system, the machine can carry out cutting and chamfering operations without removing any material, and therefore guarantees a clean and perfectly perpendicular cut and equally clean and precise chamfering, in line with the productivity and other requirements of modern extrusion lines.
The Multibell 200M is designed for the belling of PVC sewage pipes and the top-of-the-range model can achieve rates of up to 900 cycles/hour. Without altering the quality and reliability of the end product, this new solution offers various new technical features, at a lower price (of both machine and equipment) compared with the previous version: it is more compact, yet it guarantees the same productivity levels; it features an innovative system for multi-bell pipes; it has no hydraulic system; it is easy to use and it also guarantees extremely rapid format change.
The key feature of the other belling machine, Unibell 200 E&P for pressure and underground sewage pipes in PVC, is the electromechanical movement of the forming carriage. The absence of hydraulic movements means that there is absolutely no risk of oil leaking into the environment; furthermore, ordinary maintenance times are reduced. It also allows excellent energy savings, considering that electrical energy is consumed only during the actual movement of the forming carriage, and that the traditional hydraulically operated system has a much lower yield (45%). All this adds up to a faster return on the investment, greater competitiveness on the market and greater respect for the environment.