AlphaMAC aims to reduce electricity consumption
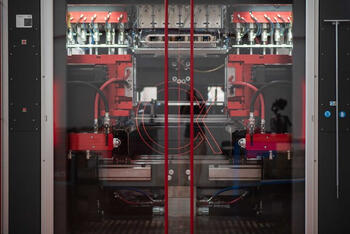
AlphaMAC has developed its range of blow-molding machines starting from the knowledge acquired from the previous experiences of two generations of electric machines and presents itself on the market with a very advanced technology regarding consumption.
One of the most current and important aspects with the evolution of technologies in the field of extrusion and blow-molding is certainly the reduction in electricity consumption, obtained thanks to the conversion of the motion from hydraulic to electric. Begun in 2006, this transformation has led today to have extremely reliable and repetitive machines, reducing drastically the maintenance linked to hydraulics (about 65% less), also eliminating the environmental impact linked to the periodic disposal of oil, and with a greater flexibility in process regulation, having many more controllable parameters available.

The surveys carried out on machines in production confirm that the average electrical consumption achieved is much lower than it was on hydraulic machines, in particular when the machine is used at its maximum capacity if we consider the consumption per kilo of extruded plastic. In fact, the most important part of consumption is linked to the heating of the resistances that keep the extruder and extrusion head at the set temperature, regardless of how many kilos the user transforms.
In a practical case, we can see how an ALPHA 800D machine, with double station, has an extremely low consumption.
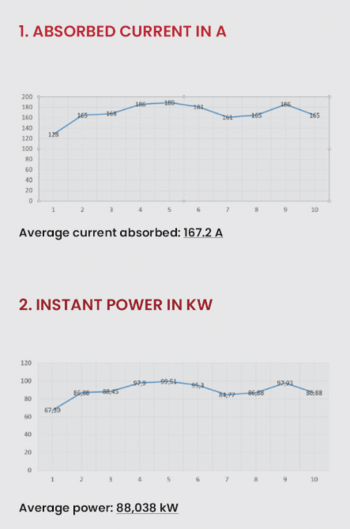
AVERAGE CONSUMPTION
0,23 kW/h/kg
Configuration: 3 layers
- external layer extruder - diameter 80 mm
- middle layer extruder - diameter 90 mm
- inner layer extruder - diameter 70 mm
Product bottle: 2.000 ml detergent with handle, net weight 62.0 g, nominal production 3.450 bottles / hour, with 6 parison head.
Test carried out: detection in production with HT MOD GSC60 network analyzer.
- calculation of current consumption, on instantaneous current absorbed with operating voltage 380V 3PH
- calculation of instantaneous electrical power
From the tests carried out and from what has been detected by the actual consumption of the machine, the average hourly consumption at standardized drive is equal to 65.2 kW/h, which reported to the number of extruded kg/h (287 kg/h) correspond to an average hourly consumption of 0,23 kW/h/kg.

In addition to the reduction in actual electrical consumption, the energy savings due to a lower use of chilled water necessary to cool the hydraulic power units of obsolete machines must also be considered. This saving can be conservatively estimated for about 1/3 of the actual consumption of a chiller that supplies water for an equivalent bottle production.
Finally, AlphaMAC favors cooling technologies aimed at significantly increasing the water flow rate in favor of a higher water temperature, a solution that offers further savings from an energy consumption point of view for mold cooling.
This result confirms the construction quality and technical choices of the ALPHA series machines, thanks to the use of the highest quality and latest generation components, reinforcing AlphaMAC position on the market as an innovative company focused on sustainability.