New VDA-M amplifier by Sensormate: one device, multiple functions
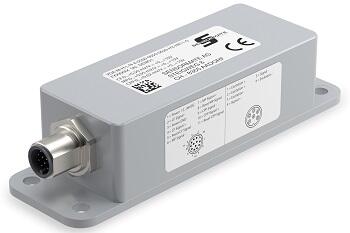
The new VDA-M amplifier developed by Sensormate - a company that is part of the Gefran Group specialising in force measurement on injection moulding and die casting machines and industrial presses - is ideally suited for use in injection moulding machines with toggle levers. VDA-M is a smart solution combining clamping force measurement, mould protection and monitoring of the cavity pressure profile.
“Tie bar strain sensors are a proven solution to control the clamping force of injection moulding machines. However, machine manufacturers and final users also face other challenges in injection moulding. On the one hand, moulds must be protected against damages caused by moulded parts that are not fully ejected. On the other hand, the pressure curve in the mould must be measured and optimally controlled to avoid faulty production results, such as burr formation or surface defects. This is usually done with the aid of complex cavity pressure measurements, whereby the sensors are mounted in the mould and must be reconnected each time the mould is changed”, stated Piero Tempini, Operation Manager at Sensormate.
Thanks to the new, three-channel VDA-M amplifier, all these functions can be performed with one sensor mounted on the tie bar or toggle, depending on the type of machine. In addition to the clamping force output, a sophisticated digital amplifier electronics provides high-resolution signals specifically conditioned for the applications of mould protection and monitoring of the cavity pressure profile.
In multi-cavity moulds, the amplifier also provides an integral curve of the cavity pressure: this provides a valid alternative requiring a lower investment than the use of sensors in the mould, which only measure a specific point and are thus not able to detect an integrated pressure signal.
Lastly, the combination of the VDA-M amplifier and GE1029 tie bar strain sensor or the SB46 model suitable for toggle mounting from Sensormate is the guarantee of a simplified installation. The independence from the sensors in the mould results in an economical, safe and user-friendly solution for optimum results in the injection moulding process.