More than an open house
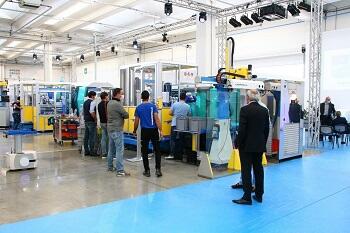
Campetella Robotic Calling 2020 took place from October 1 to mid-November. The open house event was organized in order to present two fast IML systems and the new concepts developed by the Italian manufacturer of robots and automation systems. Everything was taken care of in detail and nothing was left to chance with the aim of guaranteeing maximum safety for visitors through strict compliance with the hygiene and health regulations against the coronavirus pandemic.
The new developments have been conceived by Carlo Campetella to make the most of Lean Management and Lean Production, also in terms of Industry 4.0, focusing on new ideas, concepts and designs, thanks also to the contribution of a team of design engineers who have managed to achieve important advancements even in 2020. "We have used the past few months to bring new robot developments to series production" explains Carlo’s son Elia Campetella, general manager of the company. "The focus is on footprint reduction, precision, longevity and speed - with standardized solution concepts in modular design, implemented on various robotic and system innovations. Our corporate culture, our good reputation and our innovative strengths are our capital - also for you".
The company's medium-term prospects also include a new service concept based on augmented reality. A stand located in the immediate vicinity of the IML systems was set up for the occasion, where it was possible to experience a virtual "walk" wearing a VR headset of the last generation to have an idea of how customer satisfaction can be ensured, even remotely, by exploring all functions, components, interrelationships, parameters and much more. Similarly it was possible to discover how replacement and/or wear parts (e.g. labelling dummies) are ordered and find out how they are disassembled or assembled.
Coronavirus effect - the market situation
To date the demand for Campetella robots and IML systems has not suffered from the pandemic. The strengths of the company have had an inherently balancing effect: "The automotive sector has declined, but we have been able to compensate for this with growth in the industrial and food packaging and medical segments. Packaging automation for online sales is growing strongly, especially in Germany, a market in which we are strengthening our presence also in terms of sales and service," confirms Marco Marconi, area sales manager. As a result of travel restriction, the company took the opportunity to devote more effort to organizational changes and internal management projects.
Campetella Robotics Calling 2020
Marco Marconi underlines the marketing strategy put in place by Campetella in a few words: "We couldn't just leave it all behind! We have to stay in the market, communicate and be proactive. This is what our customers expect from us, whom we have been asking. When it became clear to us that practically all plastics trade fairs worldwide would be cancelled in 2020, including Fakuma, we changed course. Instead of meeting with customers in Friedrichshafen, we invited them to Montecassiano, 800 km further south on the Adriatic coast." To this end, Campetella exploited all that had already been prepared for Fakuma in the previous months. The negotiations with Arburg turned out positively for a clever win-win alliance.
Expectations fulfilled
Campetella offered considerably more application examples, products and information during the Campetella Robotic Calling 2020 than a large Fakuma booth or virtual show would have been able to ensure: "Anyone who visited us during these times must have already taken a very strong interest in automation solutions", adds Marco Marconi. No comparison with the 2014 Open House who welcomed around 500 visitors in three days. The new initiative inspired not only customers and partners (in alphabetical order: Arburg, Bazigos, D. Souiris, Gammaflux, Mevisco, Moretto, Simon, Viappiani), but also experts from universities.
"We were able to energetically advance an important project on Machine Learning with the University of Ancona” the sales manager says. "The interest of the trade visitors, also in our digitalisation solutions, was very high, as expected. Visitors came not only from Italy (70%), but also from Austria, Germany, the Netherlands, Great Britain, France, Greece, Palestine and Nigeria. We welcomed representatives of the general packaging, food packaging and medical industries, who - encouraged by the boom in their sectors - are now increasingly looking for automation partners". The area representatives and sales managers of the company led small groups of visitors in guided tours through the factory and the exhibition area with the support of technicians and engineers always available in the vicinity of robots and IML systems.
“Feedback and comments were highly encouraging, especially from first-time visitors, who expressed their appreciation about our strong investment in new technology, clear and straightforward engineering, as well as production and administration processes combined with the benefits of lean production, lean management and Kaizen," Marconi comments.
Exhibitions - projects for the future
"We have presented everything Campetella has to offer. We have developed a new range of robots, especially the ultra-productive Double Concept series, future-oriented control concepts, industry 4.0 compliant solutions. Machine Learning, for example, will have a great future," Marco Marconi goes on.
Robots and all other plant components are monitored by specific algorithms. Predictability of what will happen in the plant, how long it will optimally run under the given conditions and/or when a component has to be replaced. These are some of the elements of precaution and machine analysis. In the future and right now, customers can use the online portal to see how the plant works, including acceleration curves, vibrations, paths, temperatures, cycles and other characteristics. In addition, thanks to augmented reality and the VR headset, customers can move freely around the virtual system and order, for example, replacement parts.
"In simple terms, the total cost we had budgeted for the 2020 exhibitions, including Fakuma, a seven-digit amount, has been 're-labelled' to a large extent into factory modernization, acquisition of new equipment and the product and system developments mentioned above," Marco Marconi says.
"It's remarkable that one of the two IML systems was sold in the very first days of our open house exhibition. It is a cheese tubs labelling application. The system will meet the customer's requirements after minor modifications to the standardized components," Marco Marconi comments.
Campetella's IML technology can be upgraded with the addition of new modules in order to handle 16-caviy moulds: "Basically, Campetella stands primarily for fully automatic, robot-supported labelling, decoration, handling, finishing and added value for any product from any industry. Everything comes from a single source, Campetella, with identical programming standards, in the form of simple engineering solutions with high-tech content for the maximum achievable performance. This credo is our constant guide," the sales manager reveals.
Campetella - quo vadis?
"We are getting used to the coronavirus restrictions. Everyone wears masks all the time, maintaining distance. This does not really interfere with our work. The optimistic point is that our order books are full until April 2021, triggered by the fact that we have been working very hard in the markets in recent years and have established or strengthened our service centers. For example in Germany with the new Peter Nellen agency, in Hamburg, to serve the strong packaging market in Northern Germany and the expanded capacities of KT Sakkas in Aurachtal, in Bavaria, and other expanding subsidiaries or agencies in other regions such as Hunter in the USA as well as Cristian Lopez Alvarez, key account manager for Mexico. As a result, we are always able to react quickly. In any case, our Campetella Calling Open House 2020 will pay off, and the next one as well" Marconi says.
The main market areas
Giacomo Svampa, continuous improvement engineer, who also has a voice in the strategic market development division, explains: "With the CRC Customer Portal, an analysis and trouble-shooting technology in detail, we will soon have an important tool in our hands for keeping the production line in operation without downtime. All parts are coded and can be immediately identified for various purposes. Plus many tutorial animations based on ‘Creo’ and ‘Indy 40’ to configure systems, give instructions for disassembly and assembly of components such as Eoat and IML tooling. This is a bonus when generating business in the area of labelling and handling small food packaging such as capsules and cups."
As Svampa underscores, the coronavirus has changed consumer behaviour. People are increasingly preparing food at home again. For example, the consumption of margarine has grown significantly and so has the need for packaging. "However, the segment of large containers for restaurants has been shrinking. On the other hand, the order volume for labelling buckets for liquid and free-flowing products (e.g. for DIY stores) has remained stable. We recently received an enquiry of this kind from a US company that was previously unknown to us. We sent him an offer and a video of how we would handle it. The next day we had their order on the table".
The boom in the demand for medical primary packaging is also remarkable. "Here, we want to focus our efforts on sustainably meeting the demand for automation from the European regions (primarily Italy, Germany and Russia) and from overseas (USA)," Svampa states. According to him, Campetella's production capacity under current conditions is 25 to 30 standardised top-entry robots plus special systems based on the design-to-order method. The turnover breakdown is 30% Italy, 30% rest of Europe, 30% North America, 10% other markets.
"We foresee a good future for our new Stack series because of its outstanding performance," Giacomo Svampa predicts. All the core components of the proven Concept system are being employed here. The intensive use of carbon fibre components in the moving parts of the robots provides more lightness and rigidity. The system has been specially developed for the removal, stacking, packaging and logistics of products (72 x 2 = 144 cavities) in very large batches. Also noteworthy is an extremely fast robot whose cycle time amounts to 3.9 seconds despite its size.
Going back to the Open House, new developments are constantly being tested in the field of racing. For many years Carlo Campetella has been active in motorbike championships, ant took from this world the inspiration for new materials and innovative designs for lightweight construction, performance, precision, durability and speed. The visitors to the in-house exhibition appreciated the Cartesian and side-entry robots, Scara solutions, super-fast sprue and part pickers, as well as control systems and IoT interface concepts integrated into each machine.
The exhibits included two automation systems, representing the very latest in industrial robot technology, which were demonstrated live during the event applying labels yoghurt cups or fresh cheese tubs at maximum speed and precision.
An X-Series Mini-Modula compact side-entry robot from Campetella was employed for IML labelling on PP yoghurt cups. The robot was equipped with a fast and compact horizontal arm for quick label insertion and product take-out operations. A tilting axis guaranteed a hygienic process which ended with the cups being stacked upside down with their openings on the conveyor belt. An additional advantage of the Mini-Modula is its extremely small footprint. And if that is not enough, at the open house it cooperated with the new X-Series CO1 Cartesian robot: its electric servo axis is the right hand to move the stacks of cups from the conveyor to a storage box. An Omron AMR (autonomous mobile robot) took care of transporting the boxes to the finished goods warehouse. The system featured a four-cavity mould from Simon and a total cycle time of no more than 2 seconds. The injection press interlock time was 0.6 seconds only. The two Campetella robots worked hand in hand on an Arburg Allrounder 570 H hybrid injection moulding machine with a clamping force of 1,800 kN, while the L labels were supplied by Viappiani.
The utilization of labelling dummies (produced in the new 3D printing centre) is a decisive criterion for the process speed. Special pins, charged with 12,000 volts, polarized (magnetized) and positioned the labels in less than a second into the cavity where they were stabilized by compressed air to ensure a perfect fit before being applied to the container’s backside.
An X-Series Modula high-speed side-entry robot from Campetella provided the solution for labelling plastic cheese spread tubs in Bazigos' four-cavity mould. Four Mevisco cameras monitored the product quality inline and continuously. A quick label feeder with servo drive was used on the robot, which managed the 5-sided labels supplied by Viappiani. Here again, the tilting axis performed hygienic upside down stacking of the tubs on the conveyor belt. With its high payload, an X-Series SPIN3 Scara robot took the labelled stacks and quickly deposited them into a transport box. Finally, another Omron AMR was in charge of storing the boxes filled with cheese spread tubs in the warehouse. The entire automation system was mounted on an Arburg 630 H hybrid injection moulding machine with a clamping force of 2,300 kN. Labelling took place in cycle time of around 4 seconds and/or an injection press interlock time of only 0.9 seconds. The polypropylene conditioning equipment and the centralized cooling systems were supplied by Moretto.