Producing high-quality chrome grille components in a single shot
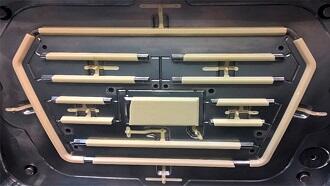
With its FLEXflow technology, Italian hot-runner specialist HRSflow has developed an innovative solution for the injection moulding of high-quality parts primarily for the automotive industry. FLEXflow is a servo-driven, finely regulated valve gate system for hot-runner systems. The precise control of the melt flow of each individual hot-runner nozzle permits a very balanced filling of all cavities and uniform pressure distribution during packing stage, even with multiple gating and widely varying cavity volumes. The radiator grille from the HRSflow test mould measuring 580 x 330 mm with a total parts weight of 297 g and different wall thickness, from 2 to 3 mm, on cavities is subsequently chrome-plated and must therefore meet very high demands in terms of surface quality. Several car component suppliers have already positively tested this ABS and ABS/PC part on their electroplating equipment. The first chrome-plating applications are due to go into series production shortly.
Different shot weights in one filling process
With the FLEXflow valve gate system, even large-area parts can be moulded with high-grade surfaces. With the cascade injection moulding process that is normally used for this purpose, the electrically driven needle valve nozzles allow the precise, sequentially coordinated opening and closing of the valve pins with variable velocity over stroke length. This in turn permits accurate control of the melt flow on each hot gate and of the volume flow in the cavity as a whole. With the customized opening of the valves, the dreaded pressure loss that occurs with conventional cascade injection moulding methods is avoided, and, with it, the accompanying marks on the moulded part. Moreover controlled position of pin during packing stage allow to reach independent pressure control on each gate and thus desired shrinkage for each cavity, speeding-up matching of tolerance requirement and avoiding expensive modification of tools.
The injection-moulded radiator grille is produced in a single shot over ten gating points with nozzles from HRSflow's MA series. The system layout consists of a compact runner and is designed expressly not symmetrical. The volumes of the cavities for the individual moulding elements of the radiator grille have a ratio of 1:20 from the smallest to the largest mould cavity, with 30% of thickness variation from thinner to thicker. The injection time is 2.9 s, the holding time is 6 s, the hot-runner temperature is 255°C and the mould temperature 60°C.
In the past, to achieve the different shot weights and still meet the demands for chrome-plating and assembly tolerances, separate moulds would have been needed to produce this high-quality part. The aim of this hot-runner system layout was to prove the strengths of the FLEXflow technology with the aid of this multi-cavity application. Nicola Pavan, CAE department coordinator and project leader at HRSflow says: "To prove FLEXflow capability we intended to mold the components only with simultaneous opening of the electrically driven needle valve nozzles with a previously defined opening stroke setting.
The volume of injected melt for each individual nozzle is accurately controlled during filling and packing by changing needle strokes up to reach desired local pressure. So we have a local control of flow rates and applied pressure and the possibility to easily balance family tools and control warpage without part or runner modifications”.
Simulation analysis with Moldex 3D
A mould-filling analysis with both the simulation programs Moldex 3D and Autodesk Moldflow calculated the optimum parameters for each of the ten nozzles of the FLEXflow system. During the injection process, every valve assumes a position that has been freely programmed by the user. The needles can be programmed using up to 8 different control points for both opening and closing, by defining velocity and position for each step. Up to two cycles of opening and closing can be programmed for each needle. The simulation analysis and practical application show very high conformity with the actual progress of the flow front in the individual cavities. "FLEXflow balances out the different shot weights in an optimum manner and fills the different part volumes of all the cavities within the same time and thus avoids issues of flash, reduce warpage and allow precise control of weld lines", says Nicola Pavan, summing up. With the FLEXflow technology, it is possible, with a short fine tuning stage, to produce parts without any surface defects even with limitation typical of family tools. This also drastically reduces the reject rate for the injection moulder. The moulded parts show reduced frozen-in stresses, are not overpacked, with controlled warpage and are ideally suited for the chrome-plating process.
Better quality parts
With FLEXflow, the individual valve pins of the currently up to 16 hot-runner nozzles can be precisely opened and closed sequentially, independently of one another. Depending on the opening or closing step, up to eight valve positions can be predefined with a motor accuracy of ±10 micrometre. Through this extremely precise positioning and speed control of the valve pins, a very homogeneous pressure distribution in the mould cavity and thus in the entire molding is attained. As result of the much larger process window, necessary clamping force and even weight of the part can be reduced without any loss of quality. In automotive construction, the FLEXflow technology has advantages in particular on injection moulding of large-area exterior and interior parts such as bumpers, spoilers, instrument panel supports (IPS), door liners, roof liners, components for the vehicle's lighting and glazing systems, headlamp lenses and panoramic roofs.