Macchi reviews its POD technology for K 2016
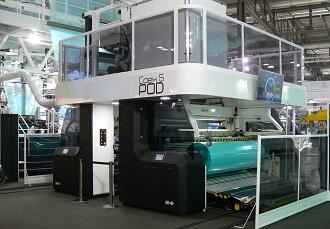
The manufacturer of blown film extrusion lines is revving its engines to face the K 2016 show, which will take place in Düsseldorf from 19 to 26 October. For the company based in Venegono Inferiore (Varese, Italy), three busy years have passed in a blink, since the previous edition of the event.
2013 was the year of the POD (PolyOlefin Dedicated) technology: 5-layers PE products made their appearance on the stage of the world market and, driven by the enthusiastic favour of the collation shrink film industry, gained quickly a substantial share of the machinery sales. Macchi, who believed and invested heavily in the POD philosophy straight from the beginning, came out as the real forerunner of this technology and, having sold more than 40 POD lines all over the world, have been dictating the pace of the evolution, and have been able to gain a considerable, unsurpassed experience which has led to the birth of a whole range of POD solutions. At the same time, the many advantages provided by the POD films have encouraged the resin suppliers to develop a number of innovative resin grades to tackle different markets, the first and foremost being the flexible packaging.
In this respect, K 2016 comes at the right time for the Varese-based manufacturer: the unexpected sale results achieved by the majority of the flexible packaging printing and converting machinery manufacturers, which introduced their products during the last Drupa, have in fact pointed out how the market is ready for another giant step ahead, under the pressure of a growing world population which is asking for more food, better preserved and packaged to satisfy a greater variety of needs.
The dynamic
packaging sector offers huge potential for technology suppliers, packaging
converters and key brand owners. A recent study by Smithers Pira forecasts its
growth at an yearly rate of 3.4% , reaching
within 2020 the value of 250 billion dollars. Flexible packaging is the
most economical method to package, preserve and distribute food, beverages,
other consumables, pharmaceuticals and products with extended shelf life. It
has to be designed with barrier properties tailored to fit the products being
packaged and their end-uses, while other barrier packaging formats generally
provide a one-size-fits-all approach.
Three main key-trends are driving the market for flexible packaging. The first one is represented by downgauging, as the combination of environmental pressures and high polymer prices make customers demand even thinner films. On the other end of the spectrum there are the ever more important high-performance films. The trend in food packaging films is towards high-performance film structures that are less permeable in order to increase shelf life and enhance flavours. A growing share of premium products, including products sold in modified atmosphere packaging (MAP), is also favourable for flexible packaging of baked goods. One of the advantages of flexible packaging is the ability to choose the barrier based on product and shelf life requirements. The third trend is represented by the consumer convenience, as more consumers lead increasingly busy lifestyles, leading them to prefer ready meals in new flexible packaging formats.
The future of flexible packaging will also see bio-based applied technologies. In the past few years, there have been a number of new product launches involving bio-based plastic packaging. Rather than focusing on polymers obtained by non-petroleum sources, the interest is toward the development of barrier films with degradability and compostability features, as these materials do not fare well into the mainstream of traditional polymer recycling. The proliferation of bio-based plastic films, such as polylactic acid (PLA) and thermoplastic starch (TPS) films, is now paralleled by G-Polymer, a compostable PVA copolymer (modified PVOH), with high barrier properties, commercially available by Nippon Goshei who also supply the necessary bonding materials.
And this is exactly the “mission” of the POD technology, and more globally of the coextrusion technologies by Macchi: to provide the flexible packaging market with, on top of its well-known characteristics, something which is quickly becoming a rallying cry: technologies for sustainability.
To meet the
growing demand for environmentally-friendly packaging Macchi, on the occasion
of the coming K show, have decided to put on display a 5-layer POD line,
running at a high production rate and processing a special formulation,
specifically designed by the Dow Chemical Company, who recently developed a
stand up pouch made from only one raw material, polyethylene. One of the most
promising niches within the flexible packaging market, this stand up pouch
offers the same convenience and performance of multi-material pouches, with the
added benefit of being recyclable, since PE bag and film recovery currently
exists. When compared to other packaging options, PE stand up pouches are often
lighter in weight, leading to decreased energy use in manufacturing,
transportation and refrigeration. The recyclability and energy efficiency of PE
stand up pouches can help a company, whether it be a manufacturer or a user, to
meet its sustainability goals.
During the entire duration of the show, the machine will provide all visitors a live proof of the fact that a POD film can be down-gauged sometimes up to 30 or 40% of the original thickness (thus saving resources, as thinner means less raw materials and less energy), is subsequently much lighter (thus reducing the carbon footprint during the packing and transport stages), and is easily recyclable (as it is made of mutually compatible resins), confirming over a number of really striking live demos that it represents an effective, highly environmentally-friendly (and cost-effective) material: the best marketing tool to allow the industry to recover some of the margins lost during the last difficult years.