Unconventional number of cavities to optimize productivity and investment
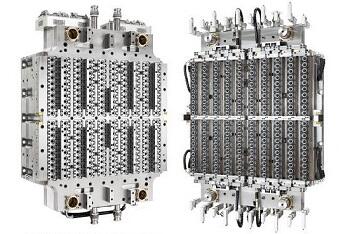
When it comes to the manufacturing of medium and large-sized PET preform moulds, a well-known rule requires that the number of cavities can be 72, 96, 128 or 144. To enable processors to optimize productivity and investment, Sipa offers a solution that squeezes more cavities into a given mould space, the result of a unique configuration of hot runners and ingenious tool engineering with absolutely no loss of preform quality.
According to Sipa a 72-cavity mould can be considered a good choice for low-to-medium output production on a 250-tonne machine like XForm 250. On the other hand, to obtain an important incremental boost, without having to invest on a bigger tooling (i.e. 96 cavities), Sipa has developed an 84-cavity mould for optimizing the productivity of the XForm 250 platform. This unconventional mould provides a significantly better output/capital ratio than a 72-cavity mould - something like 13% better in fact, when producing preforms for 1.5-liter bottles on the same XForm 250 machine - and well ahead of what is possible on rival 72-cavity machine/mould combinations.
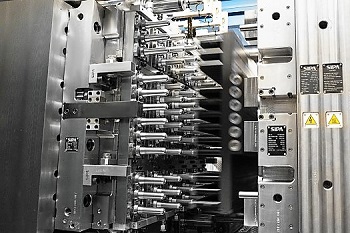
Creating a hot runner system that consistently and reliably enables more cavities to be filled identically, at high speed, without excessive force, has been made possible thanks largely to its Xflow melt distribution system developed by Sipa. Xflow incorporates an innovative hot runner manifold design that provides the best balance of melt distribution in the industry. In fact, it exhibits the lowest pressure drop ever measured. This technology, unique to Sipa, allows the company to create very high-cavitation systems without having to compromise on balance, pressure losses, and the formation of acetaldehyde due to polymer degradation.
Sipa applied the same engineering solution to develop the world’s first 180-cavity injection mould combined with a 500-tonne XForm 500 machine. This is now also available with a 200-cavity mould producing over 130,000 preforms per hour.