Over 1000 HRSflow’s servo-driven hot runner systems sold worldwide
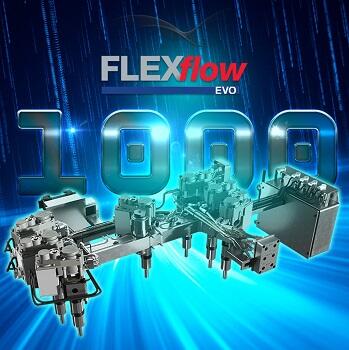
A steadily growing number of injection moulders are being convinced by the precision and reliability of HRSflow's hot runner technology, which has been proving its performance in many industries for years. First introduced at K 2013, their servo-driven valve gate system has since been a powerful driver of growth for this hot runner specialist, making it one of the world's number one automotive supplier today. Now the number of units sold around the globe has passed the 1000 mark. The wide range of applications includes automotive engineering with lighting, interior, exterior and under-the-hood applications, increasingly also electrically driven vehicles, as well as logistics and environmental, household and gardening.
As part of its continuous development, HRSflow recently launched Flexflow Evo, a new generation technology that features reduced space requirements (cutouts) in the mould thanks to optimized geometry. In addition, melt pressure and flow rate can be adjusted even more easily thanks to the flexible control system. What has remained unchanged is the perfect part surfaces that can be achieved, even in sensitive applications such as film back-moulding.
The use of Flexflow Evo in cost-reducing family moulds provides particular advantages. These are currently attracting great interest because they can be used to produce different parts in a single shot. To outline the potential of the system in live demonstrations, HRSflow has produced what is now the third family mould for the simultaneous production of elements of the interior door trim of motor vehicles. It shows how the filling process can be perfectly balanced and warpage largely controlled despite very different moulded part sizes, something that has often been problematic with family moulds. At the same time, it demonstrates that the flow rate, which can be set independently and precisely for each cavity, reliably prevents overfeeding and flash formation. HRSflow makes the three demonstrator moulds available to customers for trials, material tests and training at the company's headquarters in San Polo di Piave (Italy), at the plant in Hangzhou (China) or at the plant in Grand Rapids (Michigan/USA).
Maurizio Bazzo, President of HRSflow, comments: "Today’s automotive manufacturing environment is experiencing a transition phase towards a new direction: design complexity, e-car development, lightweighting and digitized driving. At the same time Tier 1 suppliers and OEMs are looking for overall cost saving processes. To obtain the next-generation high quality parts and to reduce scrap rate the market will need increasingly flexible flow control for part moulding optimization. HRSflow is ready to face this new challenge."