Easy processing of regrind from thermoforming
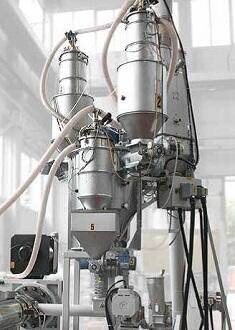
EasyFeed is the new feeding system offered by Amut in combination with the EA - 52 D extruder, to process up to 100% of regrind material during the in-line thermoforming whithout compromising the main extruder flow rate. During the sheet extrusion process, the presence of the regrind recycled from the thermoforming skeletons reduces the bulk density of the material fed to the extruder. This reduction is largely variable depending on the content of regrind material and the skeleton thickness.
EasyFeed feeding system
The Easy Feed system makes it possible to monitor and adjust the extruder specific flow rate regardless of the regrind’s bulk density and content. Easy Feed mainly consists of:
- a mixing and handling unit for the polymers and additives fed to the extruder;
- a horizontal-axis dosing system, bivalent type, which underfeeds the extruder screw in presence of high bulk density materials and overfeeds it in case of low bulk density materials;
- an integrated automation system with handling parameters, which are adjusted automatically, based on the variations in the bulk density of the melt fed to the extruder.
EA - 52 D extruders
The extruders belonging to the 52 D series, named after the length of the plasticizing unit, feature an innovative feeding zone design guaranteeing high performances and excellent quality standards. The 52 D (diameters) of the plasticising unit’s name result from the combination of the 40 diameters which feed, heat and melt the polymer, with the 12 diameters needed to degas and push the material towards the die.
Maintaining the 40 D length for the first part of the screw (a tried and tested size for plasticizing screws without degassing system) made it possible to design a less aggressive geometry for a more gentle material handling. The energy supplied in this part of the screw is optimised to reach the correct melting rate required for the subsequent degassing stage. The screw’s dispersive and distributive mixing elements, together with the high efficiency of the newly designed feeding zone, ensure low variations in terms of specific flow rate and, therefore, melt material temperature in case of changes in the revolutions per minute.
In the 12 D screw section, the degassing unit is set up to optimize the extraction of volatile substances from the melt. The subsequent and last section of the extrusion screw produces the pressure required to push the material through the filtering screens and feed it to the gear pump at the correct pressure rate, with the lowest energy absorption.
The main new features involve the feeding system, the melting and mixing process performed by the plasticizing screws, and the degassing zone configuration. All of this results in high efficiency, low investment costs, excellent versatility, minimum maintenance and reduced energy consumption.
Extrusion becomes easier
Thanks to the combination between the EA - 52 D extruder and the EasyFeed system, technologies and know-how merge together to make the line easy to use and flexible during the production process. This system can process all the regrind thermoplastic materials used in the thermoforming phase, be they light or heavy, with a bulk density lower than 200 kg/m³ (deriving from the grinding of skeletons with thicknesses down to 0.15 mm,) or with a bulk density of 650 kg/m³ (deriving from the grinding of skeletons with thicknesses exceeding 2 mm).