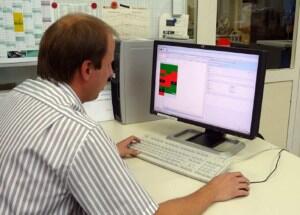
I sistemi di esecuzione della produzione (MES, Manufacturing Execution Systems) forniscono l'interfaccia tra la produzione e la gestione aziendale che, collegando in rete le macchine e rendendo più trasparenti i processi, consente ai trasformatori di migliorare efficienza e qualità dei propri manufatti. Il sistema MES e-factory 2 di Engel, sviluppato appositamente per lo stampaggio a iniezione, è stato adottato proprio a tale scopo da Geberit, presso il suo stabilimento di Pottenbrunn, in Austria. "L'obiettivo era quello di abbattere i tempi di attrezzaggio dei nostri impianti e migliorare in maniera costante i processi produttivi, aumentando la loro trasparenza", ha commentato Michael Höchtl, ingegnere di processo di Geberit, a proposito della decisione, da parte dell'azienda, di installare il sistema MES e-factory 2, versione a cui Engel ha aggiunto nuove funzioni.
Geberit, la cui sede principale si trova a Rapperswil-Jona, in Svizzera, si colloca tra i principali produttori e fornitori europei di componenti e impianti idrosanitari. Il gruppo impiega circa 6100 dipendenti in tutto il mondo, 350 dei quali presso lo stabilimento di Pottenbrunn, dove 39 presse a iniezione con forza di chiusura tra 40 e 600 tonnellate consentono di realizzare un'ampia gamma di manufatti. Dal momento che le misure delle filettature e dei raccordi variano da un paese all'altro, lo stabilimento produce un totale di 1300 articoli diversi. Ciò comporta cambi stampo frequenti, nonché un elevato numero di parametri da impostare.
"Prima di iniziare a utilizzare e-factory, impiegavamo un dischetto per ciascuno dei 1300 articoli prodotti. L'operatore addetto all'attrezzaggio della macchina doveva prima di tutto reperire il dischetto giusto e, successivamente, stampare una copia cartacea dei dati", ha spiegato Höchtl. Oltre a richiedere tempi estremamente lunghi, questa procedura comportava un elevato rischio di errore, dal momento che ad alcuni articoli era associata più di una versione, con più di un set di dati di attrezzaggio.
"Ma e-factory ha messo fine a questo circolo vizioso", ha aggiunto l'ingegnere. Attualmente 28 presse a iniezione sono connesse a e-factory 2 con l'aggiunta di 1100 nuovi set di dati, mentre le macchine e gli stampi meno moderni, ormai impiegati molto raramente, sono stati al momento esclusi dalla rete. "La gestione centralizzata dei set di dati relativi ai vari articoli ha comportato uno straordinario incremento dei livelli di produttività in un arco di tempo estremamente ridotto", ha sottolineato Höchtl. Il modulo dati di questa soluzione MES consente di gestire i set di parametri relativi ai singoli manufatti in maniera centralizzata e, successivamente, di inviarli alle presse a iniezione in linea. Esiste un solo set di dati attivo per ciascuno stampo, e qualsiasi modifica apportata a uno di essi viene memorizzata nel relativo registro.
Geberit si serve inoltre di un secondo modulo offerto da Engel, al fine di assicurare l'ottimizzazione costante del processo. Il modulo Monitor invia direttamente all'ufficio del responsabile produzione gli indicatori prestazionali e le informazioni di stato rilevanti, oltre ai dati relativi all'avanzamento della produzione, le cause degli eventuali fermi macchina e i possibili allarmi. Ciò consente di rispondere tempestivamente a qualsiasi deviazione rispetto al piano di produzione, in molti casi ancora prima di produrre pezzi difettosi. Il precedente sistema di monitoraggio PDA indicava soltanto se una macchina era in attività o meno, mentre e-factory 2 informa anche del motivo di un eventuale arresto della produzione. In questo modo, è possibile analizzare le cause a monte dell'errore e acquisire importanti informazioni che successivamente consentono di ottimizzare i processi.