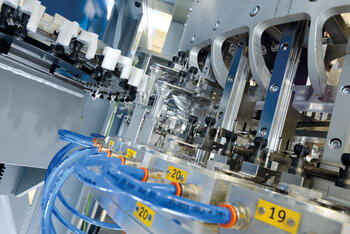
Si chiama Xtreme Sincro l’impianto integrato per la produzione di bottiglie in PET presentato da Sipa a Brau Beviale, la fiera dedicata al settore delle bevande svoltasi a Norimberga dall’11 al 13 novembre. In un unico sistema vengono combinati l’inietto-compressione di preforme e lo stiro-soffiaggio (ICSBM) delle bottiglie, unendo la flessibilità dei sistemi bistadio con la convenienza di quelli monostadio.
“Abbiamo deciso di creare l'impianto di produzione ideale: compatto, flessibile, facile da usare, con un consumo energetico estremamente basso, capace di trattare il PET nel modo più delicato possibile per mantenere alta la qualità del materiale, di manipolare le preforme senza danneggiarle e di produrre le bottiglie più leggere sul mercato, riducendo così la quantità di PET utilizzato, pur mantenendo prestazioni straordinarie. Con Xtreme Sincro, crediamo di aver centrato il nostro obiettivo”, ha dichiarato Enrico Gribaudo, direttore generale di Sipa. Il progetto è stato realizzato grazie allo strumento finanziario Life dell’Unione Europea e fa parte di un programma globale per promuovere lo sviluppo di tecnologie che aiutino l’industria a risparmiare energia e a ridurre le emissioni di anidride carbonica in atmosfera.
Con il sistema di inietto-compressione Xtreme è possibile produrre preforme fino al 10% più leggere di quelle ottenute con lo stampaggio a iniezione convenzionale, senza che ne risentano le prestazioni. Mentre fino a poco tempo fa il rapporto massimo ottenibile tra lunghezza e spessore di parete di una preforma era pari a un valore di poco superiore a 45, tale rapporto adesso può arrivare a 80. L’inietto-compressione supera i problemi relativi alla produzione di preforme con pareti molto sottili, grazie a stampi che si aprono leggermente quando inizia l’iniezione e si richiudono dolcemente per completare l’operazione. Questo consente di ridurre la pressione d’iniezione e la forza di chiusura, (favorendo anche una maggiore durata dello stampo), lo stress sul materiale fuso, che si traduce in livelli ridotti di acetaldeide, e la caduta della viscosità intrinseca della resina.
Il sistema Xtreme risulta più versatile, riduce i tempi di cambio stampo e migliora la qualità della preforma. Grazie alla configurazione rotativa e all’azionamento pneumatico si integrata bene con il soffiaggio rotativo del sistema di nuova generazione SFR EVO3, più veloce, versatile ed efficiente rispetto alle versioni precedenti. Con il nuovo design delle camme può essere ottenuta una produttività di 2250 bottiglie all'ora per cavità, che attestano il sistema tra i più veloci sul mercato. Il nuovo e più compatto blocco valvole risulta ancora meno ingombrante.
L’impianto si contraddistingue per un’elevata efficienza grazie a diversi fattori. Innanzi tutto, il sistema di inietto-compressione impiega temperature inferiori rispetto a quelli di iniezione tradizionali, riducendo il consumo energetico del 10% circa. Inoltre, le preforme non devono essere raffreddate subito dopo la produzione e il riscaldamento prima del soffiaggio risulta molto ridotto. Infatti, i forni convenzionali con riscaldamento a raggi infrarossi sono stati sostituiti da piccoli forni a induzione e ad alta efficienza. Il riscaldamento è diretto soltanto sotto il collo delle preforme.
Proprio come il sistema di produzione Xtreme, la macchina SFR EVO3 si contraddistingue per un nuovo dispositivo standard di cambio stampo, veloce e facile da usare. È anche molto più semplice convertire la produzione da contenitori standard a quelli per riempimento a caldo. Infatti, mentre il circuito di riscaldamento rimane nel porta stampo, quello di raffreddamento è incorporato nella cavità. È necessaria solo una semplice modifica di quest’ultima cavità per passare da un tipo di contenitore all'altro, mentre il porta stampo rimane in posizione.
Il sistema integrato Xtreme Sincro può essere collegato direttamente a una riempitrice, sviluppata sempre da Sipa, per configurare una linea completa, che dall’iniezione delle preforme, passa al soffiaggio e termina al riempimento. Il sistema può essere completato con i sistemi di imballaggio secondario e di pallettizzazione prodotti sempre dal costruttore veneto, così da ottenere una linea di imbottigliamento completa da un unico fornitore.