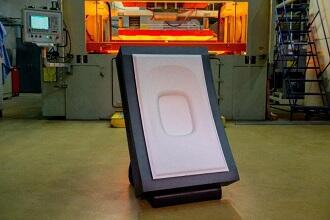
Alla recente Formnext 2018 (Francoforte, 13-16 novembre), grande risalto è stato dato da Sabic ai suoi materiali per la manifattura additiva. In questa direzione va il filamento EXL AMHI240F per FDM (modellazione per deposizione di fuso), caratterizzato da elevata resistenza all’impatto e adesso disponibile anche in colore bianco, oltre che nero. La sua formulazione, che comprende un composto esclusivo PC-silossano associato a una colorazione ottimizzata, offre una resistenza all’urto fino a quattro volte superiore al policarbonato standard e una modalità di rottura più duttile nei pezzi stampati, come è risultato nella validazione delle prestazioni dei materiali e come è stato mostrato attraverso diversi articoli esposti per dimostrare la versatilità del filamento.
Sono stati presentati anche i filamenti FST, che, contraddistinti da facilità di lavorazione e ridotta tossicità ed emissioni di fumo, sono in grado di assecondare i requisiti delle applicazioni aerospaziali OSU 55/55. Il filamento di Extem è invece stato proposto le potenziali applicazioni che richiedono maggiore resistenza alle alte temperature rispetto al filamento di PEI Ultem. Sabic sta anche sviluppando un materiale avanzato che integrerà i filamenti di grado aerospaziale Ultem AM9085F. Il nuovo filamento di supporto offre il vantaggio di un più rapido distacco dalla struttura di sostegno per pezzi con geometrie complesse, contribuendo a ridurre i costi delle post lavorazioni.
La gamma di compound rinforzati Thermocomp, comprendente materiali a base di resina PEI Ultem, è stata proposta per la produzione additiva di grande formato (LFAM) attraverso cui ottimizzare applicazioni quali, per esempio, gli stampi per alte temperature in autoclave per il settore aerospaziale, quelli riutilizzabili per prefabbricati in cemento e una vasta gamma di stampi per termoformatura di pezzi di grandi dimensione a temperature più basse, tutti in grado di ridurre costi, tempi di realizzazione, magazzino e pesi rispetto ai tradizionali stampi in acciaio. Lo stampo per la termoformatura di un pannello per interni aeronautici presentato in fiera era realizzato in Thermocomp AM EC004XXAR1, grado a base di resina Ultem rinforzato al 20% con fibra di carbonio.
Oltre a quelli per realizzare tali tipi di stampi, Sabic sta lavorando per validare diversi materiali per la manifattura additiva di grande formato di prodotti finiti quali Olli, il primo minibus elettrico al mondo a guida autonoma. In fiera è stato esposto il parafango del veicolo, stampato utilizzando uno dei compound della gamma Thermocomp.
Infine, per la SLS (Sinterizzazione Laser S) selettiva, Sabic sta sviluppando nuove polveri con cui superare alcuni tradizionali limiti delle resine amorfe in questo processo, come l’incompleto consolidamento degli strati, la densità troppo bassa dei componenti, l’incostanza dimensionale e proprietà fisiche non ottimali. Con le nuove soluzioni è possibile produrre pezzi in materiale amorfo con densità superiori al 96% e buona stabilità dimensionale. In fiera sono stati presentati articoli ottenuti in PC sperimentale mediante SLS per mostrare i vantaggi derivanti dall’uso di tale materiale rispetto a quello di PA 12, quali migliori proprietà termiche, buone prestazioni meccaniche, minore spreco di polveri e stampabilità di pareti sottili e piccoli dettagli.