Prepregs on the fly
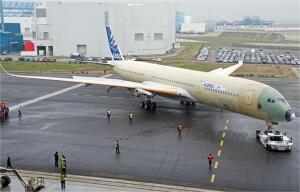
When the Airbus A350 XWB takes to the skies for the first time in a few months it will be a momentous achievement both for Airbus and Hexcel, the composite materials producer that, in 2008, obtained the contract to supply carbon fibre prepregs for all the A350 XWB composite primary structures.
The A350 XWB is the first Airbus with a structure that is over 50% composites, whereas composite materials constituted only 15% of the structure of the A340 and 23% of the A380.
Its composite structures built with the HexPly M21E prepreg resin matrixinclude entire fuselage panels, keel beam, the entire wing (covers, spars and centre wing-box) and empennage (tail assembly).
The lower wing covers are the largest single civil aviation parts made from carbon fibre, measuring 32 metres long and 6 metres wide.
To produce the vast quantities of prepregs required for the A350 XWB, Hexcel introduced a new model for the cost-effective large scale production, producing resin film in a continuous process to very tight aerial weight tolerances in Duxford (UK), which it says has improved the quality, accuracy and consistency of the resin film.
The resin film from the UK is converted into UD prepreg at Hexcel facilities in France, Spain, Germany and the USA from where it is supplied to nearby Airbus facilities.
This has resulted in a highly effective supply chain model for prepreg production with shorter lead times, greater responsiveness, reduced transportation of materials, point of use delivery, less packaging, reduced inventory and fewer requirements for cold storage space.