Block vs cast
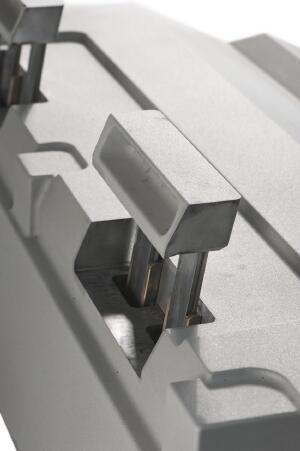
A thermoforming mould manufacturer, Self makes its products using almost exclusively aluminium castings, which is considered the most convenient solution. The sheet thermoforming process, taking advantage of cast or machined aluminium moulds, is adopted in the manufacture of small batches of medium and large size parts whenever quick setup times and low initial equipment costs are required. At the moment, says the manufacturer, the necessary condition for ensuring the high quality level required for a thermoformed part is the application of cast moulds made of top-rate aluminium instead of moulds machined from an aluminium block. In particular for design products, even with quality castings without surface porosities or defects, it is possible to obtain mould finishing levels comparable to those of machined moulds.
An additional advantage associated with the use of cast thermoforming moulds is represented by the heating and cooling coils inside the mould: in cast moulds, the coil ducts are incorporated into the casting according to the shape of the part, as a result improving the heat transfer between the internal medium and the aluminium mass.
In the specific foundry process, the ducts are accommodated inside the casting mould and are surrounded entirely with melt aluminium at a constant thickness. On the contrary, in machined moulds the thermal exchange is ensured by ducts installed into grooves that are milled on the back side of the tool. As a consequence, more energy is dispersed into the air, while there is also a significant reduction of the surface contact between the duct and the aluminium. Alternatively, deep drilling can also be used, which however does not adapt to the part's shape as a result leading to thermal non-uniformities.
The use of casting techniques for innovative and tailor-made solutions was adopted by Self above all for the manufacture of components with undercuts and/or in the case of modular moulds, implementing removable modules and inserts.