BMW innovates thanks to Piovan
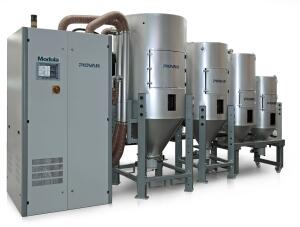
Out of the testing period, that last six months, at which five major suppliers of auxiliary equipment took part, Modula of Piovan was regarded by BMW as the best solution, for its utmost efficiency of operation, energy utilization, auto adaptability and constancy of process conditions. In detail, for one of the new German production sites of the very innovative BMW i3 and BMW i8, when at the initial project stages, BMW specified to all potential suppliers that any of the processes necessary to convey, dry and blend the different polymers in use, had to be energy efficient and self sustainable. Also, the output claimed would be tested and compared, to assess and subsequently determine the ranking of performance. Modula is the innovative auto adaptive and energy efficient drying system with multiple hopper assembly and the two set ups supplied to BMW were configured to also support an expansion to twelve production lines, from the current six.
The materials utilized by BMW are mainly blends, with polypropylene or polycarbonate base, like PP/EPDM and PC/SAN. The plastic part is first injection moulded and immediately transferred to the painting lines, a very sensitive phase of the production process where silicone particles are banned. One very important feature of Modula is the absence of silicone components/parts within the system, making it fully suitable for applications such as the one of BMW. The two sets are configured with single dry air generator and seven drying hoppers with volumes ranging from 600 to 1,000 litres.
Each hopper requires specific conditions for optimum operation (dry air flow, temperature and pressure) depending on the different material characteristics, such as the type, the required initial and final level of moisture, the hourly material consumption and the granule size. A safety condition is systematically adopted and the drying system is inevitably sized based on the most critical processing parameters, such as maximum material consumption, at maximum temperature, with the highest airflow. This basic model goes against any principle of energy efficiency and certainly does nothing to reduce or optimise the system running costs. The two Modula systems automatically adjust and control all operating parameters for each individual hopper and hence use only the overall amount of energy strictly required. This is made possible through a specific control software that interfaces the settings for each hopper with the data collected by the sensors installed on the system. This means that, by using a Piovan patented airflow measuring device, located in the air supply line and at each hopper, the airflow can be adjusted and controlled instantaneously and individually, hopper by hopper. In addition, the total airflow is modulated automatically and efficiently by the central drying unit, equipped with IE3 class blowers, resulting in optimum process operating conditions.
Modula is available for medium and large capacity applications (200 to 2,000 kg/h) and provides energy savings of as much as 50% with respect to ordinary centralised drying systems of equivalent capacity. Modula is Winfactory ready. Along with Modula, BMW was supplied by Piovan with Varyo auto adjustable vacuum conveying systems, MDW gravimetric blenders and Winfactory supervisory system.