Corotating twin-screw extruders for recycling and compounding
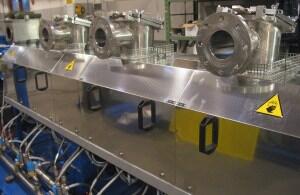
The use of Comac corotating twin-screw extruders in the recycling sector has increased in recent years, after a long period during which they were employed mainly in plants for the production of masterbatch and for compounding. Indeed, the less expensive single-screw extruders are often preferred in non-critical straightforward recycling applications, in which the use of co-rotating twin-screw extruders is not justified. However, the latter are now increasingly being used in two other two major applications. One is the recycling of post-consumer PET bottle flakes that, thanks to the high degassing capacity guaranteed by the co-rotating twin-screw extruder, can be processed without drying (the result is a material suitable for a range of different applications, for example, the production of fibre or of sheets for thermoforming and regrinding applications); the other is the recycling of materials derived from polyolefin-based industrial waste.
While Comac's plants have always been used in the compounding of polymers containing different types of fillers and reinforcements, the use of special configurations, such as, for example "tandem" ones (i.e. consisting of two cascade extruders separated by a filtering system), has emerged as the ideal solution for carrying out recycling plus compounding of materials that are very difficult to process, such as films that have been heavily printed with solvent-based inks. Plants of this kind allow the extraction of volatile matter, highly effective filtering, the addition of virgin raw materials, fillers and masterbatches etc., and regrinding, thereby producing a high-quality recycled and filled material. All of this would be difficult to achieve using single-screw extruders.
For PET recycling, the company generally offers lines with diameters of between 40 and 44 mm, equipped with 3 vent zones featuring more or less high vacuum systems, depending on the desired end-product characteristics. For polyolefins, on the other hand, the tandem configuration is obtained through a first extruder (where the plasticisation of the material to be recycled, an initial degassing step, and melt pre-filtering take place) and a longer extruder to which the melt is then transferred and where virgin or less contaminated materials, coloured masterbatches, fillers and additives are added; this extruder is fitted with side feeders, various atmospheric and vacuum degassing points, a final filtering device and a die-face pelletiser.
The company offers several versions for processing post-consumer PET bottle flakes without drying. These feature extruders with diameters ranging from 40 to 120 mm, which allow output rates of 100-130 kg/h and over 1500 kg/h. The 70-mm model, offering output rates of 500-550 kg/h, is the one most frequently produced. In the recycling of polyolefin waste, the 120-mm version offers output rates in the region of 2000 kg/h; these rates are even higher with the new 135-mm model which was recently added to the Comac range.