Injection moulding of metal alloys
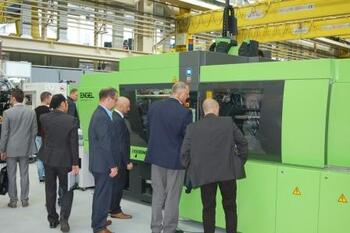
With Liquidmetal, Engel opens the door to completely new classes of material and product characteristics; metal alloys can now be efficiently injection moulded. As the exclusive machine manufacturing partner of Liquidmetal Technologies (Rancho Santa Margarita, California), Engel is the only provider worldwide to offer system solutions for the injection moulding of Liquidmetal materials.
The machine manufacturer presented this technology to the public at the Engel Symposium 2015, from June 16 to 18 in St. Valentin (near Linz, Austria), for the first time. More in detail, an electric machine e-motion 110 (see picture) injection moulded parts for medical forceps.
The difference between a Liquidmetal machine and a conventional injection moulding machine for plastics processing lies mainly in the injection unit. The Liquidmetal alloys are available in the form of slugs cut from round rods. These blanks are automatically fed into a melting chamber where the material is melted inductively until 1000°C under high vacuum conditions. Instead of a screw, the machine has a piston with which the molten metal alloy is injected into a thermo-regulated mould. The 2-cavity mould installed on the e-motion 110 was manufactured by the Italian company Saga, which had also its own stand inside the exhibition area dedicated to 44 Engel’s partners at the symposium.
Liquidmetal stands for a class of material with completely new characteristics. The zirconium alloys feature an amorphous, i.e. non-crystalline, structure, which is why they are referred to as metallic glasses. Components made from these materials are extremely hard, but at the same time very elastic, which leads to very good recovery behaviour. In order to process these materials using injection moulding, Engel has developed a new machine based on the tried and tested all-electric machine series e-motion.
With Liquidmetal, Engel is presenting an alternative to metal injection moulding (MIM) and CNC processing, which provide ready-to-use parts with a very high surface quality in a single step and in short cycles. The Austrian machine manufacturer sees good potential for this technology in the field of medical technology. Furthermore, there is a broad range of application in the fields of electronics, aerospace, military technology and sports equipment. It has already found a first area of application in the entertainment electronics and watch industries.