New generation cast lines for stretch film
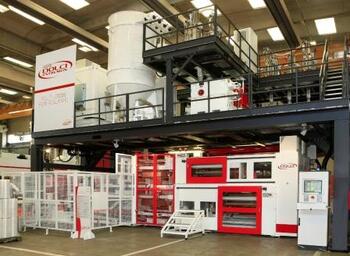
At the Plast and Ipack-Ima fairs, Amut Dolci Bielloni presented a range of new generation cast lines - a result of the technical synergy created when Dolci Bielloni was recently acquired by the Amut Group. Indeed, Amut’s numerous years of experience in building extruders made it possible to innovate the concept of conventional extrusion incorporated, until now, into cast lines for stretch film: during an open-house event, held in May and coinciding with Plast 2015, processors were able to see, in operation, a line capable of achieving a constant production rate of 750 metres per minute.
The new concept consists of a 7-layer configuration with 6 extruders, and it is available in a 2-metre version and a 3-metre width version, with net hourly outputs of 1500 and 2400 kg, respectively. As regards the main innovations introduced, first of all, the extruders have water-cooled engines and gears featuring a forced oil circulation cooling system, while the screws have an increased length (L/D = 40) for greater homogeneity and flow rate. The cooling unit is equipped with a double cylinder with a large diameter, specifically designed for the production of “Super Power” films. The high-speed winder can reach a constant speed of 800 metres per minute for the production of automatic and manual jumbo reels, guaranteeing excellent quality and perfect geometry.
The line also stands out for compactness (both versions have a general footprint of about 121 square metres), for its low energy consumption, amounting to 0.4 kW/kg, which also covers the needs of the water circulating unit as well as of the trim recovery system, and for its ability to produce reduced thickness (10 micrometres). Furthermore, the distance between the chill roll and the winder is extremely short, in order to facilitate its start-up.
Trim recovery is achieved through direct feeding of the fluff into the extruder tube; this operation is performed “cold” and is contamination free. A special system of filters guarantees complete absence of dust during the accumulation of the fluff which, even during plant start-up, is stowed in a dedicated silos and subsequently recovered during the process. The plant layout has been optimized and the extruders, and relative screen changers, are positioned parallel to each other, to save space and allow easy maintenance and changing of the filters. The operator has a dual control unit, and can therefore work in proximity to both the chill roll and the winder. Before being unloaded, each reel is individually weighed to check that it is within the set parameters; in this way, anomalies detected are signalled allowing the plant to self-regulate automatically.