AEM takes the heat
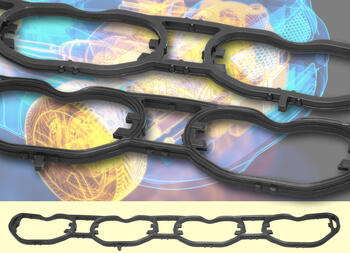
At DKT//International Rubber Conference (Norimberga, June 29 - July 2, 2015), DuPont Performance Polymers (DPP) introduced Vamac VMX5000, a new and commercially available family of ethylene methylacrylate elastomer (AEM) pre-compounds that extend the upper temperature limit for AEM applications by 15 to 20°C - offering heat resistance as yet unmatched in AEM, coupled with a long-term improvement in static heat ageing. The new Vamac AEM pre-compounds, currently under evaluation by major auto OEMs and Tier 1 suppliers for seals and gaskets, air management system applications and high-temperature coolant hose covers, are expected to offer a viable alternative to fluoroelastomers (FKM) at significantly lower cost and lower specific weight, in a temperature range between 160°C to 190°C - especially where standard acrylic, ethylene vinyl acetate (EVA) or AEM elastomers are no longer considered. “We developed Vamac VMX5000 to fulfil the latest auto industry needs for materials that can withstand more aggressive, engine environments. The new Vamac pre-compound does that by pushing the upper AEM in use temperature, and offers a very cost-effective solution”, said Patrick Cazuc, global marketing manager for Automotive at DuPont Performance Polymers. “It also underlines the DuPont commitment to expanding the Vamac family of AEM products that help auto OEMs and Tier 1 suppliers meet engine efficiency targets, particularly in air management systems”, Cazuc added. Vamac VMX5000 is designed to meet new challenges to automotive hoses and seals imposed by new industry trends such as high-pressure turbo charging, exhaust gas recirculation and other technologies requiring resistance to higher temperatures and aggressive fluids. It also exhibits improved acid and base resistance compared to bisphenol cured FKM compounds, a feature of increasing importance for parts in contact with new oils containing aggressive additive packages or “blow-by”. Additionally, products in the Vamac VMX5000 series incorporate a new filler system enabling much easier production of coloured non-black parts, leading to better optical colour control combined with superior compression set resistance. Recently, DPP also launched Vamac VMX2122 AEM, a new dipolymer for wire and cable applications offering better physical properties and processing performance than current AEM DP dipolymers, combined with enhanced colour stability. It also meets existing sealing and hose specifications for AEM terpolymers, and thus can be used in applications where diamine cured terpolymers cannot be used.