PX all-electric machines: made-to-measure
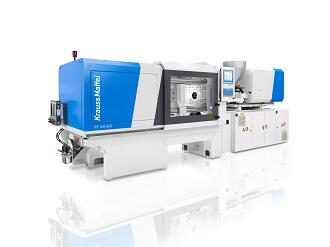
The new PX all-electric made-to-measure injection moulding machines introduced by KraussMaffei at K 2016 feature an unprecedented combination of the advantages of an all-electric solution with maximum modularity.
Electric injection moulding machines are known for precision and efficiency - and for admittedly limited equipment options. "Until now, customers have most often been forced to decide between low-budget and high-end designs. KraussMaffei is now presenting the first all-electric machines on the market, which the customer may tailor to its specific manufacturing needs in the modular principle in the hydraulic area. This includes, for example, larger platens, faster injection speeds, more ejector force or the ability to be operated with food-grade NSF H1 lubricants," explains Hans Ulrich Golz, managing director of KraussMaffei and president of the injection moulding machinery segment at the KraussMaffei Group.
The K 2016 featured the launch of the all-electric toggle machine with clamping forces from 500 to 2000 kN. It was conceived and designed with flexibility in mind, and this extends over the entire service life from the purchase to everyday production to retrofitting. The tried-and-tested modular concept of the KraussMaffei hydraulic series was thus transferred successfully to the all-electric PX.
The great adaptability is demonstrated by two essential features of the series. First, the injection and clamping unit can be combined individually from a wide range of variants. Secondly, versions of the PX come standard with the larger platens of the respective next higher clamping force. These intermediate models are identified using odd numbers, i.e. PX 51 to PX 161. The larger clearance corresponds to an increased maximum mould weight, approximately 750 kilograms for the PX 51 compared to 450 kilograms for the PX 50. Since the machine bed of the PX is split, clamping and injection units can also be combined as necessary. Large clamping units, small injection units. In production, this means that no more space is taken up than what is absolutely necessary for the production order. There are five high-performance injection units available for each clamping unit. Each injection unit has its own performance level and can be fitted with one of three to four different screw diameters.
The basic properties of all-electric machines have been set up to meet the desire for flexibility, since electric motors function independently of each other. This allows for any number of processes to run in parallel, ensuring high speeds. The three main axes of the PX for the injection unit, plasticizing unit and clamping unit are driven by air-cooled servomotors, making the PX exceptionally economical in terms of energy and water consumption. All servomotors also work in what is called "recuperative mode," where brake energy is converted back into electricity. As a result, up to 60 percent of the brake energy can be temporarily stored and used by the machine itself or fed back into the power supply.
The slave
axes of the PX, meaning each axis for the injection unit and ejector movements,
operate using servo-hydraulics in the default version. The initial movement
takes place via two parallel injection unit barrels because this enables nozzle
contact forces to be built up very quickly and free of lateral forces, unlike
the movements carried out with only one electric
barrel. For particularly high material throughput, for example in the case of thin wall injection molding, there is an option for increasing the injection speed for the PX to more than twice the normal speed, thereby increasing the plasticizing output significantly. The injection unit can be set up to swivel in order to make it easier to change the non-return valve or replace the screw.
For the ejectors, the reason behind the servo hydraulics relates to durability. Electric drives are sensitive to the mechanical impacts that occur when plastic parts are demoulded using a vibrating platen. Any customer that does not do this during production and requires even more precision has the option to equip the PX with an electric ejector drive.
“Three things matter when it comes to the clamping unit: geometry, force and speed. In all three areas, the PX offers options for coordinating the machine to meet individual requirements”, explains Golz. As already mentioned, the size of the platens can be increased with the odd-numbered intermediate models, meaning that the entire machine bed of the machine that is next in size is then used. This ensures that the high mould weight
receives the necessary linear support. Thanks to the extremely wide support of the moving platens on linear guides, a precise parallel movement is always achieved. The tie-bars are released and thus are always free of lubricant and clean. The clamping unit bed has been designed so that the entire area under the clamping unit, lengthwise and crosswise and all the way to the floor, remains free for failure and parts logistics. As a result, parts containers or conveyor belts can be rolled under the machine very easily and practically, without any cross-beams getting in the way. The maximum mould height can, if desired, be increased to 100 millimetres more than the respective standard version. For instance, it can be increased from 450 to 550 millimetres for the PX 120. The mould height adjustment itself takes place automatically. Regardless of whether they use hydraulic or electric power, ejectors need plenty of force for parts that shrink onto the cores. This is why the product range provides an option to increase the ejector force by 50 percent. For projects with aggressive cycle times, there is an ejector speed of 700 millimetres per second as opposed to 350. In continuous operation, the PX features an ergonomically favourable working height of 130 cm, which remains the same for all clamping forces, ensuring perfect accessibility of the mould and nozzle for setup or during production. The resource consumption of energy and water is extremely low. Precision and availability, on the other hand, are high.