Unveiled the small 25-tons ECS SP
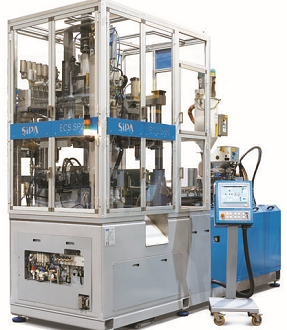
Sipa has unveiled the ECS SP 25, the latest and smallest in its family of injection stretch-blow moulding (ISBM) machines for small and medium-sized production lots. The machine, with a 25-tonne injection clamp force, joins two established family members, the ECS SP 50 and ECS SP 80. All three have four stations, one each for injection, conditioning, blowing and discharge. Together, they complement Sipa’s high-output ECS HS and FX single-stage systems.
All ECS SP machines have special design features that make change-over between different product configurations quick and simple. In addition, they all take up little floor space and are very energy-efficient. ECS SP machines also handle preforms in a way that makes it possible to mould neck and shoulder designs not feasible with two-step technology. Integrated production of preforms and bottles ensures scratches-free surfaces on the finished products.
The ECS SP family is therefore ideal for use by converters wanting containers with high-quality appearance and non-standard necks, in limited production batches and in various colors - the sorts of requirements frequently found in the cosmetics, pharma, personal care, food, liquor, and miniatures businesses. Bottles can be made with contents as small as 10 ml, typically used for such products as pharmaceuticals and also shampoos and lotions found in hotel rooms.
The ECS SP models use hybrid drives: hydraulics where large forces are required (to apply clamp force during preform production, for example) and servo-electrics for fast, precise and energy-efficient movements (opening and closing of the blowing unit, plasticizing screw rotation, index rotation). This combination helps the machines achieve a carbon footprint smaller than rivals. Another key feature of the ECS SP 25 (in common with the ECS SP 80) is that it accepts moulds originally designed to run on equipment from major competitors.
Other important features of the ECS SP 25 include: a best-in-class lock-to-lock time; a very competitive investment/output ratio and hence bottle cost; higher cavitation capability than rival machines of a similar size (at least 25% higher for the same size of container); ceramic heaters for faster heating and excellent material distribution for oval shaped bottles - without having to rely on costly and complex shaped injection tools; superior mould quality based on over 30 years of experience in single stage mould production at Sipa; a valve-gate hot runner system as standard, capable of feeding moulds of up to 10 cavities; and - last but not least - a very robust construction and very smooth operation for durability and repeatability.